Table Of Contents
What Is Assemble To Order?
Assemble to Order (ATO) is a production model certain manufacturers follow, where the final production begins only when a customer places an order. As individual product parts or subassemblies are ready, manufacturers only put these standardized parts together, assembling the final product as and when they receive an order.
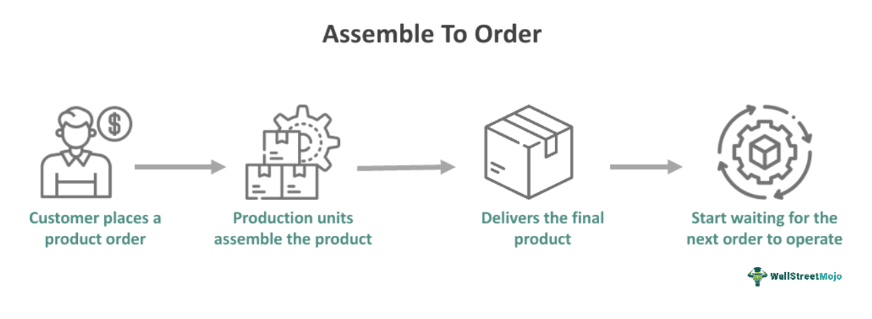
The ATO production strategy is adopted by companies that offer customers a wide variety of customized products. These businesses let customers choose products per their preferences. However, the customization is standardized, i.e., customers can choose from standard options. Once customers place orders, the company assembles the order. This process typically enables quick deliveries at reduced costs. Therefore, this model is usually not suitable for bulk manufacturing.
Table of contents
- Assemble to Order (ATO) is a production model in which sub-assembled parts are gathered, and final or finished products are assembled and completed only when a customer places an order.
- Companies that adopt such models prefer to offer customers customized products aligned with their requirements. Some popular companies using this methodology are Ferrari, Dell, etc.
- It combines make-to-stock and make-to-order production strategies.
- A company may apply different production models based on the type of products and services they deal in. It is possible to have multiple production techniques in one company.
Assemble To Order Explained
Assemble to Order is a production methodology in which the final product is assembled and built only when a customer orders it. Different manufacturing processes and models are adopted by companies, depending on the industry and the product they manufacture. Manufacturers who wish to leverage economies of scale and engage in mass production do not usually find this manufacturing style suitable. This system is suitable for companies that cater to a certain target audience and customer base and do not mind variations in business volume.
The assemble-to-order definition indicates companies only follow this manufacturing model when they wish to offer tailor-made products per the buyer's requirements. One of the key aspects of the ATO model is that it reduces the costs of capital, which ultimately works to the company's advantage. Since companies undertake jobs based on customer requirements and work specifically on a single product, quality expectations are high.
Companies may follow other production models besides the highly flexible ATO manufacturing style. Depending on the product and industry requirements, they may modify manufacturing strategies from time to time.
Examples
Below are two assemble-to-order examples that facilitate further discussion.
Example #1
Suppose a high-end car company sells cars to a specific demographic. They specialize in building customized cars with top-quality engines, high performance, and top-notch features. Peter, a reputable businessman, wants to buy a car and places an order with the company.
When the company receives Peter’s order, the manufacturing team studies the specifications, such as the color, seats, doors, etc., and initiates the production process. The company already has standard parts, subparts, subassemblies, and other inventory. They assemble the car and deliver it to Peter.
Example #2
Computers are one of the most common products manufactured using the ATO production scheduling model. While most reputable computer, tech, and hardware manufacturers use this production method today, Dell earned a solid reputation by selling built-to-order computers directly to customers much before any other player could find steady ground in this area. In the years preceding the Y2K bug, Dell towered over every other company in the tech space, including Apple, posting huge profits via built-to-order computer sales.
Advantages And Disadvantages
The advantages of the assemble-to-order process are:
- A significant reduction in the cost of production is typically observed since products are scheduled for manufacturing only when an order is placed.
- Companies need not invest in mass or bulk production processes. They can accommodate market trends or changes swiftly during final assembly, ensuring funds are not locked in at the production stage.
- Customers benefit from this model as they get custom-built products based on specific usage or application requirements.
- Once an order is logged in, companies can estimate the delivery time with precision since standard parts, subparts, and subassemblies are ready and only assembled upon order receipt.
- The optimized manufacturing process registers low or nil inventory or raw materials wastage.
The disadvantages of assemble-to-order manufacturing are:
- Companies using the ATO model operate largely on customer demand. Hence, anticipating or predicting customer demand on time with some level of precision is important.
- A low customer or market demand may result in low revenue generation for the company.
- Companies following the ATO model employ significant resources to keep inventories undamaged and whole. This may increase expenses even when no orders are in sight.
- If the supply of parts, subassemblies, or other key components is affected, the order fulfillment process is adversely impacted.
Assemble To Order vs Make To Order
Here are some key differences between ATO and make to order manufacturing processes.
Basis | Assemble to Order | Make to Order |
---|---|---|
Mode of Operation and Inventory Readiness | Products are assembled from intermediate parts and subparts when a customer places an order. The inventory is ready. | Products are produced or made from scratch when a customer places an order. The inventory is not ready. |
Time of Manufacturing | Manufacturers await sales orders to begin work. Standard customization is possible. | Products are manufactured upon receiving customer orders. However, as the inventory is not ready, manufacturing begins upon order receipt. Extensive customization is possible. |
Manufacturing Completion Timeline | Manufacturing is usually completed before orders are received. Once orders are placed, only assembly is required. | Depending on the business volume, manufacturing is an ongoing process as the product is produced from scratch. |
Frequently Asked Questions (FAQs)
In operations management, ATO is a scheduling strategy. The manufacturer keeps standard parts ready, prepared to handle orders customers place. It helps regulate operations based on demand without investing in bulk production.
The risks of assembling to order are:
- These companies must have some tolerance level with respect to quickly accommodating market changes and evolving customer preferences.
- Companies using this model must be ready to tackle risks pertaining to low order volume, heavy production issues, a lack of supply of parts and subassemblies, and consequent revenue loss.
- Products manufactured through the ATO model may prove expensive, indicating they cater only to certain customer demographics. This may limit market reach.
The common components in ATO are semi-furnished, subparts, subassemblies, intermediate and fabricated components, and packaging materials. These parts are gathered in bulk and kept in inventory in anticipation of new orders. When a customized order is placed, the parts are assembled to deliver the final product.
Recommended Articles
This article has been a guide to What Is Assemble To Order. Here, we explain its examples, compare it with make to order, and advantages and disadvantages. You may also find some useful articles here -