Table Of Contents
Flexible Manufacturing System Definition
A flexible manufacturing system is a manufacturing concept that allows production to adapt when facing changes in its requirements. The required changes could involve the amount of product being produced or a new product part that is needed. The changes could be either predictable or unpredictable.
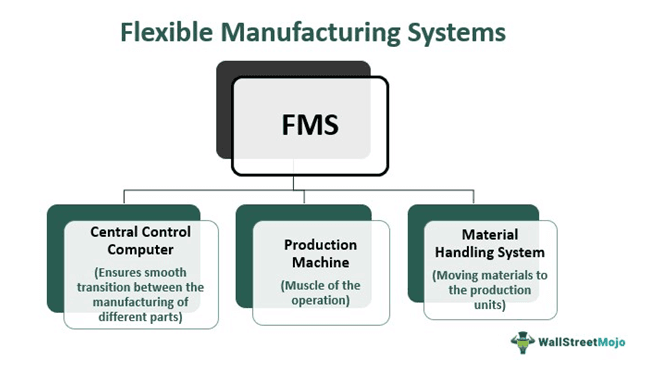
The system will typically involve automated computers capable of reacting to changes in production. The systems’ flexibility allows companies to enhance their efficiency and lower the costs typically associated with manufacturing. In short, an FMS system improves a manufacturer’s overall agility in production.
Key Takeaways
- The flexible manufacturing system is a manufacturing concept that allows the machines and other components to adjust rapidly when required.
- These systems will typically involve a central control computer, production machines, and material handling systems.
- There are differnet types of FMSs based on their level of flexibility, type of operation, and number of machines used.
How Does Flexible Manufacturing System Work?
A flexible manufacturing system could be machine flexible, material handling flexible, or operationally flexible.
The world is becoming closer than ever with advancements in technology and trade. This generates stress on companies engaged in international trade or otherwise. The demand for certain products has skyrocketed as companies now have to face the challenge with innovative, high-quality solutions produced in large numbers, some of them with a heavy scope for customization.
This has led businesses to look for new solutions to ramp up production while remaining flexible enough to change the output when needed. One such solution is the flexible manufacturing system capable of automating production without sacrificing the ability to change output when required.
Flexible manufacturing systems can work in several different ways depending on the production needs of an individual business. However, these systems will typically consist of three main functions that allow the system to remain operational. These include:
- Central Control Computer
- Production Machines
- Material Handling Systems
These three functions will work together to allow a smooth transition of information and functionality from one component to another. Understanding how the flexible manufacturing system works is like comparing the different functions of human body parts – the brain, muscles, and blood.
Central Control Computer
The central control computer will be the brains of the operation. It will be in control of the transition between producing different parts and changing the amount of production. The transition to making different parts must be a smooth and rapid process.
The central control computer should also overcome malfunctions to allow for uninterrupted manufacturing, although this function can change from system to system. This function is vital to tell the other systems how to transition from one another.
Production Machine
The production machines are the muscle of the operation. They will be the computer numerical control (CNC) machinery or robots that take orders from the central control computer. These highly automated machines can change tasks rapidly when needed. This process assures production is each part as per the requirements.
The production machines connect to the material handling systems to receive the required materials to produce a specific part. At this stage, 3D printing machines are becoming more popular for their ease of use and added functionality.
Material Handling Systems
The material handling systems are similar to the nutrients in the blood sent to the muscles to keep them moving and functioning properly. They will be moving the materials to the production machines to keep making the products.
This part of the system is critical in getting the right materials to the right places.
Types of Flexible Manufacturing Systems
#1 - Based on the operation:
Since many industries are vastly different, various types of flexible manufacturing systems can cater to a diverse range of production schemes. These include:
Progressive (Line)
The production machines will be set up in line with a progressive and flexible manufacturing system. In this case, the materials will usually flow in one direction, passing the part along as it develops.
Loop
The loop flexible manufacturing system is relatively straightforward, with the materials moving in a circle going in one direction. As a result, the parts keep moving and transferring themselves to other stations.
Ladder
The ladder FMS will look similar to a ladder where different workstations represent the ladder’s legs. The workstation will then operate and transfer the part to the next workstation or leg.
Open Field
The open field layout is a little more complicated than the other flexible manufacturing systems. It involves the passing of parts to various stations, such as the production machines. These layouts will typically be for more advanced products, as they will involve additional substations.
Robot Centered
As the name implies, this flexible manufacturing system will involve robots to complete a task. The most popular use for robots is to feed the materials and transfer them from one station to another.
#2 - Based on machine numbers:
Flexible manufacturing systems can also be classified by the number of machines it uses.
Single machine cell: Uses just one machine.
Flexible manufacturing cell: Uses two or three machines and loading or unloading stations.
Flexible manufacturing system: Comprises of four or more machines connected to a common distribution system.
#3 - Based on the level of flexibility:
The level of flexibility can be different for different FMSs.
Random: Advanced system that can handle significant changes in part configuration
Dedicated: A fixed product design that produces a specific part configuration.
Engineered: Manufactures the same mix of part configuration all the time.
Modular: The manufacturer can expand the system flexibility according to need and progress.
Examples
Flexible manufacturing systems are in use all around us without us even registering. Besides, they are helping companies become more efficient by saving on production costs. These systems can also be helpful when a company has to make a product or products that are customizable.
Example #1 - Auto Parts
Since vehicles require so many different parts, they are a perfect example of a business model that can benefit from implementing a flexible manufacturing system.
In the auto industry, the amount of material they can handle and process through the production line limits the production. This can lead to significant constraints and an interrupted production line in some cases.
Manufacturing interruptions are unacceptable for most publicly traded automakers as they have specific targets set they must meet. If not, investors will want to know what happened.
The company can benefit from using an FMS system and keep the flow of materials (parts) moving through the production line. Doing so can create a seamless experience where processes such as assembly, testing, inspection, and packing can be completed uninterrupted.
Example #2 - Customizable Consumer Goods
Custom-made goods for each customer will also benefit from a flexible manufacturing system. In most cases, these make-to-order products will only begin production when the customer places an order instead of having the products stocked.
As the production process begins, it can follow specific orders from the central control computer to precisely define what needs to be customized. The material handling system will also have the ability to feed the correct materials to complete the customer’s order.