Table Of Contents
Six Sigma vs Lean Six Sigma
Key Differences | Six Sigma | Lean Six Sigma |
---|---|---|
1. Meaning | Six Sigma ensures the desired quality in processes and products by taking the appropriate actions. | Lean Six Sigma involves the goal of Six Sigma and Lean principles. It is a methodology that eliminates waste and, at the same time, looks at quality assurance. |
2. Central Focus | The central focus of Six Sigma is reducing defects and improving quality by eliminating any variability in the process. | The central focus of Lean is eliminating waste in the process while maintaining quality standards. |
3. End Focus | Six Sigma focuses on reducing defects, improving quality, and meeting customer needs. | LSS focuses on improving production methods, reducing waste, and meeting customer needs. |
4. Approach | Six Sigma is a program that can involve altering the organizational culture to prioritize quality improvement efforts. | Lean Six Sigma is a philosophy and program that aims to reorganize the culture and behavior among employees to prioritize waste reduction and quality improvement efforts. |
What is Lean Six Sigma?Â
Lean Six Sigma is a combination of Six Sigma and Lean principles. Six Sigma strives for perfection by reducing process variability, and Lean eliminates waste. The project uses a structured method to approach problems and find solutions through a series of actions described as DMAIC.
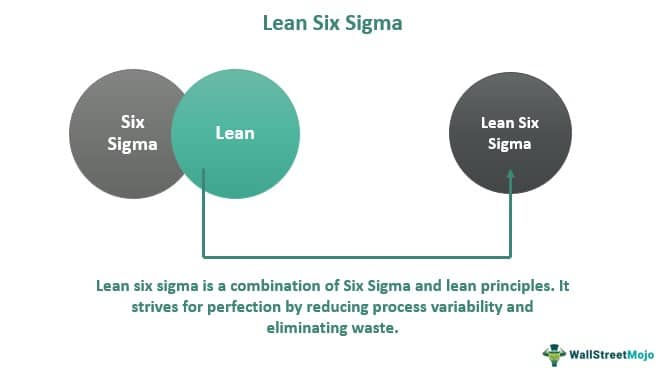
It combines both approaches to produce a practical strategy for organizational process improvement. It helps ensure that goods and services are delivered on schedule and up to client standards. Profit is increased by expanding capacity. In short, it improves and accelerates processes, eliminates product or process defects, and reduces cycle times.
Key Takeaways
- Lean Six Sigma is a combination of Six Sigma and Lean principles. It strives for perfection by reducing process variability and eliminating waste to generate effective results.
- LSS must be combined because Six Sigma cannot significantly increase process speed or decrease invested capital. Neither can Lean alone bring processes under statistical control.
- Companies benefit greatly from LSS execution by ensuring that goods and services are delivered on schedule and up to customer standards.
- Other advantages include enhanced customer satisfaction, lower expenses, higher revenues, and increased organizational effectiveness.
Lean Six Sigma ExplainedÂ
Lean Six Sigma (LSS) combines Lean and Six Sigma methods to generate effective results. The execution of the Lean Six Sigma project uses an organized approach called 'DMAIC' to solve problems. The abbreviation DMAIC stands for Define, Measure, Analyze, Improve, and Control. Six Sigma is a quality improvement approach developed at Motorola in the 1980s. It is a disciplined process improvement methodology that instructs firms to concentrate on creating and providing nearly perfect goods and services. It is a statistical term used to measure how far a process deviates from being perfect.
Lean Thinking is another methodology to improve quality and productivity developed in Toyota Production Systems (TPS). It is based on eliminating waste in processes, leading to productivity gains and improved speed and flow in the value stream. Through the elimination of wastage in the value stream, it can be described as the unrelenting search for the ideal process. Lean identifies three types of waste: loss of time and materials or resources, unevenness or variation, and overburdening of workers or systems.
Lean Six Sigma is a structured methodology for process improvement that is meticulous, data-driven, and goal-oriented. It combines two majorly recognized industry methodologies. Lean and Six Sigma processes and techniques are combined to create a powerful engine for enhancing quality, effectiveness, and speed in every business area.
The combination of Lean and Six Sigma resulted in the creation of Lean Six Sigma. Lean and Six Sigma must be combined because Six Sigma cannot significantly increase process speed or decrease invested capital. Neither can Lean alone bring processes under statistical control.
PrinciplesÂ
The following are the key principles of LSS:
- Customer focus: In any product or service, the needs and desires of the customer should always come first. Establishing a clear quality standard that is based on what the market or customers want early on is important. Any change businesses wish to implement should have the customer's best interests as its main objective.
- Identification of problems: Gathering data about the problem areas and focusing on refining those areas is essential. Any attempts to widely alter the business or its product may affect the LSS process. A comprehensive workflow is necessary to identify which processes add value and which do not.
- Remove waste: Cutting out inefficient processes is essential and the next step. After determining the issue, the business should start thinking about how to reduce the likelihood of errors. These gaps frequently manifest as drawn-out, complex procedures that offer plenty of opportunities for error and waste. It is a great technique to achieve efficiency and quality control and streamline or eliminate these procedures.
- Team communication: Effective communication of the new standards and procedures to the employees is crucial when making any change. Additionally, all employees should receive training, and businesses should value their input. All team members must be knowledgeable about LSS, aware of the project's objectives, and be updated on its status according to the fundamentals of Lean Six Sigma. Employees can also acquire certification and Lean Six Sigma belts according to proficiency. Lean Six Sigma belts come in various colors and depict progress levels in the certification.
- Flexibility: Lean Six Sigma and change go hand in hand. It is necessary to improve or eliminate a process or function that is flawed or inefficient. With LSS, sticking with a failed strategy is not an option. Change can be difficult and uncomfortable, but it is a modest price to pay to be more competitive.
ExamplesÂ
Example #1
Dan is the owner of an electronic device manufacturing company. Even though it is doing well, the company is not on par with other companies in the industry. He decides to analyze his company's problems and finds them out. He employs the Lean Six Sigma methodology and tastes success. In addition, he also provided lean six sigma training to his employees. As a result, the company achieved the following through the employment of Lean Six Sigma tools:
- Improvement in design by finding out the problems the previous one had.
- Improvements in the quality control process.
- Reduced lead time for new products.
- Reduced defects in the products.
- Reduction in scrap rates
- Reduction in maintenance costs
- Improved employee involvement in achieving goals due to Lean Six Sigma training.
- Increased customer satisfaction through improved services
- Increased profit.
Example #2
Jacobs Solutions Inc. is an American company that provides professional services internationally to a wide spectrum of clients worldwide, including businesses, organizations, and governmental bodies. In addition, the company offers engineering, technical, professional, and construction services and scientific and specialty consulting.
Jacobs Engineering Group's customers benefit from adopting Lean Six Sigma processes. The customer initiatives that used Lean Six Sigma to reduce cycle times and operational costs were highlighted in their 2004 Annual Report. In partnership with Chevron Texaco Exploration and Production Company, they have operated several oil fields in California for seven years.
Using Lean Six Sigma technologies, their ongoing improvement initiatives aimed to lower Chevron Texaco's operating costs and enhance their capital stewardship program. The company cut the time for installing engines in half using Lean Six Sigma methodologies, which saved money. In addition, the Air Force Materiel Command Inspector General's team gave AEDC a perfect score, the first for any 14 U.S.-based Air Force Materiel Command facilities in more than five years.
BenefitsÂ
- It helps reduce waste.
- As a direct consequence of reducing waste, there will be cost savings.
- Lean Six Sigma tools help in leveraging processes. With training, employees will learn to use the resources more efficiently.
- Errors are reduced through efficient and quality process administration.
- The versatility of being applied to any industry: manufacturing, services, health care, or any other industry.
- Increased employee involvement is also a benefit that is often ignored. Employees recognized for their work are happier and more enthusiastic about the company's goals.
- One of the major benefits of LSS is increased customer satisfaction. When high-quality products and services are delivered, customer satisfaction also increases. This directly translates into an increase in the revenue of the business.