Table Of Contents
Total Quality Management Definition (TQM)
Total quality management (TQM) is a standard management practice wherein each employee within an organization continually analyzes its production processes to improve the manufacturing quality of products and services and enhance customer satisfaction. It involves conducting management training and implementing analytical methods to identify and remove problem areas in business operations.
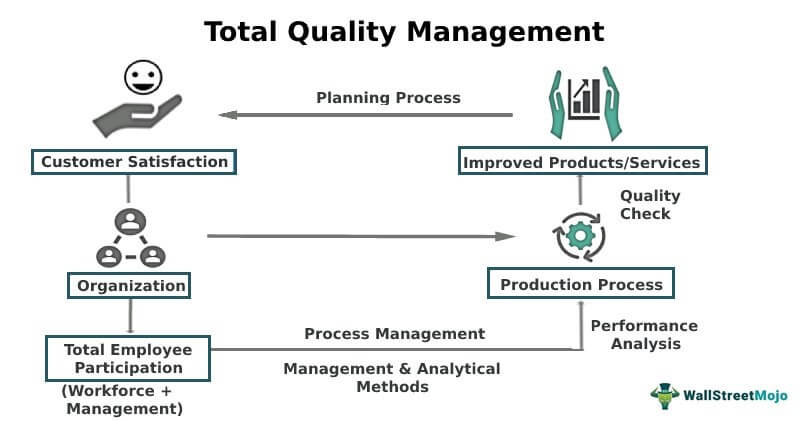
It is a successful management approach commonly employed in industries, such as manufacturing. As part of the quality improvement planning process, the executives train the workforce from different departments about the process standards and define business goals. Not only does TQM help an organization meet customer expectations, but it also helps them minimize operating costs by reducing resource waste due to insignificant practices.
Key Takeaways
- Total quality management meaning refers to an approach wherein each employee at every level in a business is accountable for evaluating products and services per quality standards and customer needs.
- TQM emphasizes that quality assurance is a shared responsibility that affects all aspects of a company or organization.
- Customer focus, employee involvement, integrated system, process-centric approach, systematic flow, continual efforts, fact-based decision-making, and relationship management are the eight principles of TQM.
- Guaranteed customer retention, increased productivity, enhanced stakeholder relationships, improved organizational culture, etc., are some of the benefits of adopting and implementing TQM.
How Does Total Quality Management (TQM) Work?
The ever-evolving and competitive global market make it difficult for a business to dominate the market. Also, the availability of the same types of products from different brands provides customers with multiple options. Therefore, consumers rely on some parameters, including cost, brand popularity, after-service, etc., to decide which product they should buy. Of these, quality always remains the deciding factor.
A quality product, in short, equals customer acquisition and retention. Since every organization adopts a customer-centric business strategy, quality assurance becomes essential in delivering the best product or service.
American statistician Dr. W. Edwards Deming, who proposed sampling-based quality inspection through his Statistical Quality Control theory, first conceptualized the TQM strategy. He also contributed toward introducing quality control in the quality management measures of the Japanese manufacturers in the 1950s post-World War Second. It became popularized as a total quality management concept in the later years.
TQM enables organizations to align their workforce with the manufacturing processes to find and eliminate errors to improve the overall quality of their outputs. In doing so, the top management, middle management, and executives assess the end products from every aspect and devise quality production plans accordingly. To prevent or eliminate errors caused by human mistake or faulty system, they take various measures, such as:
- Detect the issue and prevent it from occurring.
- Pass it on to the value-added chain for further quality inspection.
- Stop the production if the errors recur at any stage.
- Deploy the technological support.
Aside from that, TQM assists organizations in streamlining supply chain management and checking for the legal compliance of the products manufactured. In short, they want to make sure that the final product is up to the market standards, legal requirements, and customer expectations.
TQM Examples
Example #1
Plasto Toys manufactures plastic toys for kids. The brand managed to acquire a good reputation in the market, and parents relied on it for quality products. However, the regular environmental campaigns on plastic pollution affected the sale of the toys to a great extent, causing the company to incur huge losses.
As a response to this, the company management and executives agreed to implement the TQM approach for manufacturing toys using biodegradable plastics. The marketing department started advertising and promoting how their toys are harmless to the environment. In just a couple of months, Plasto Toys regained its original position in the market.
Example #2
This work talks about the “plan-do-check-act” cycle adopted by AtlantiCare, a healthcare provider in New Jersey. It helps one understand TQM at a deeper level.
With 5,000 employees spread across 25 locations, the firm implemented the TQM approach. It involved each individual from every level to provide vital feedback about the healthcare products manufactured. It led to the top-to-bottom improvement of the products as the concerned human resources took part in the quality assurance process. They observed each product from all perspectives, including customer service, people, process, workplace, etc.
As soon as they implemented the TQM strategy, the healthcare unit initiated its orientation and training program for the new employees. Also, it introduced a crash course to ensure that they understand the company strategy to maintaining quality standards.
This structured approach boosted the company revenue, which rose from $280m to $650m. It further indicated the increased level of satisfaction among the patients.
Principles of TQM
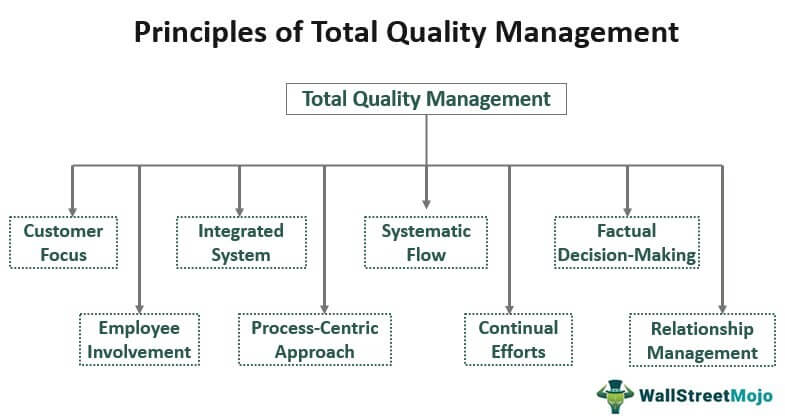
#1 - Customer Focus
Every organization strives to serve only one purpose, i.e., customer satisfaction through quality products and services. Hence, the first among the total quality management principles is customer focus. It means the end product must meet the demands and needs of the customers.
#2 - Employee Involvement
When implementing TQM, organizations need to create an environment where their employees will feel empowered. They, along with management, become responsible for assessing the quality of the products and services at their levels. Here, organizational communication plays a vital role in boosting employee morale.
#3 - Integrated System
Having an integrated system is a must for an organization to implement a TQM strategy across its business processes. Therefore, incorporating quality standards like ISO 9000 standards could help produce quality products and services. It will lead to meeting or exceeding consumer expectations as well.
#4 - Process-Centric Approach
A product or service reaches the market after passing through different processes. It means it is monitored and assessed at each production level and not only at the final stage. Process-led thinking is a sign of effective TQM.
#5 - Systematic Flow
TQM is all about strategic planning to achieve quality excellence and business objectives. Thus, considering a systemic flow would ensure the products and services are passing through every stage in the quality production process.
#6 - Continual Efforts
Quality improvement should be a continuous process. Once done and then left would only mean gradual deterioration in the manufacturing standards. For the TQM approach to prove effective, people at every level need to be alert in being regular with quality checking.
#7 - Factual Decision-Making
The organization must make fact-based decisions because every employee is participating in the quality evaluation processes. Analyzing the organizational performance using performance data, such as sales, profit, and customer retention could result in more accurate decision-making.
#8 - Relationship Management
A well-maintained relation with stakeholders like customers and employees will ensure proper quality control procedures and honest feedback. With TQM, organizations can establish effective communication with all of them and implement result-oriented changes.
Benefits of TQM
Let us have a quick look at the benefits of the TQM:
- Error prevention and elimination
- Guaranteed customer retention
- Reduced service costs and increased profits
- Feedback from all stakeholders
- Involvement and empowerment of employees at every production level
- Improved market image
- Customers becoming the main focus
- Meeting consumer expectations leads to increased customer satisfaction
- Improved organizational culture
- Enhanced stakeholder relationships
- Boost in employee morale
- Continuous efforts to meet the quality standards
- Increased stakeholder value
- Innovative strategies and creative ideas