Table Of Contents
What Is Process Centering?
Process Centering is a methodology companies use to improve business outcomes by increasing uniformity and consistency across business processes and enhancing quality control and process management protocols. This helps companies meet defined goals or specifications by managing, adjusting, and improving the features or attributes of a product or process.
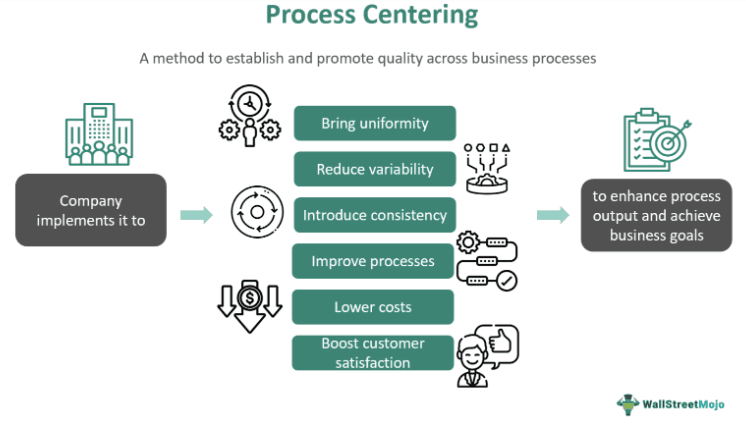
It helps processes become predictable, stable, and capable of meeting customer satisfaction goals. The technique involves enhancing standards, aligning processes with customer requirements, and decreasing resource wastage (time, money, and manpower). It is vital to quality management and continuous improvement across industries. It is an integral part of Total Quality Management (TQM).
Key Takeaways
- Process Centering is part of the continuous improvement methodology implemented to achieve quality control, waste reduction, cost control, operational alignment, and customer satisfaction objectives.
- It is a powerful tool that reduces variability across processes and products and enables businesses to meet specific objectives that improve profitability.
- It promotes employee engagement and company-wide accountability while reducing paperwork, process redundancy, and communication gaps.
- It also improves collaboration within a company, which results in better departmental and business performance.
Process Centering In Business Explained
Process Centering, a continuous improvement technique, involves modifying processes in a way that the average process output matches the target value. It is a methodology devised to manage and organize business operations using well-defined and optimized processes. This process can be represented through a normal distribution or a bell-shaped curve.
It also covers process map creation, alignment of technology with business needs, and determining Key Performance Indicators (KPIs). By following this methodology, companies can reduce waste, lower the rework rate, and boost efficiency. As performance metrics are defined, every process participant or contributor precisely understands their role. This technique is closely related to Six Sigma and statistical quality control.
It focuses on the end-to-end management of systems, procedures, and processes in an organization. Process centering outlines the links and connections between different processes and guarantees alignment with the overall objectives and goals of a business. It has various positive implications for businesses like:
- A business can successfully streamline operations plus decrease waste, resulting in increased cost savings and productivity.
- It ensures high quality and constant service delivery, allowing organizations to enhance customer service. This typically boosts customer satisfaction and loyalty.
- It enables companies to make informed decisions by providing a clear picture of the factors impacting business performance.
- Through this approach, companies can increase their risk management capabilities, which further facilitates business continuity.
- Due to the focus on continuous improvement, processes become flexible. Hence, incorporating changes based on evolving market or customer needs is possible.
This methodology is valuable in service-oriented industries, where coordination is important to reach set goals. Such companies typically have multiple tasks, stages, or activities. Hence, the impact on efficiency and business performance is significant. As productivity increases steadily and costs decline, an organization’s revenue and profitability numbers improve.
ExamplesÂ
By adopting this approach, companies can accomplish overall operational objectives and, subsequently, commercial success. Let us study some examples in this section to understand how it works.
Example #1
Suppose Joanna, a customer of Old York Bank, requests credit worth one thousand dollars. The request is handled via a data entry system, where Alex forwards Joanna’s loan application to the credit department for credit score assessment and further processing.
The credit department then gathers statistics and input from various sources, checks references, and studies the credit report. Upon analysis, Joanna’s application is proven worthy of approval. After her loan request is okayed by the credit team, the application is sent to the credit supervisor, Lily, for final approval, signature, and processing. Once Lily authorizes it, the application comes back to Alex, who initiates credit disbursement.
This process usually takes around 15 days. Therefore, the bank manager plans to implement process centering to streamline operations and reduce the loan approval duration from 15 to 4 working days. To achieve this, the bank manager considers the following:
- Strengthen data collection rules
- Automate major tasks at every step
- Develop a system for the simultaneous processing of the different tasks associated with a loan application across multiple departments
- Lay down specific communication guidelines and protocols for the departments handling loan applications
In this way, Old York Bank can improve its loan application processing through process centering.
Example #2
According to an April 2022 article, Ence developed and implemented a system to promote and achieve operational excellence across several biofactories, with a specific focus on improving every stage of the production process. It included process optimization from the raw material to the finished goods stage.
Processes, data, and digitization were announced as the cornerstones of their optimization plan, as outlined in the article. The key areas of improvement included:
- Process and product improvement plans, where all operating variables were to be handled and streamlined for maximum productivity and efficiency.
- Achieving quality and customer satisfaction objectives was another targeted milestone.
- Focusing on standard operating procedures and personnel training was also high on the list of improvements.
- A noteworthy feature of this endeavor was the application of Artificial Intelligence (AI) devices and tools to achieve business objectives.
This illustrates how every industry plans to leverage process centering to maximize profits and profitability.
Advantages
As process centering promotes continuous improvement, it offers many benefits to companies, teams, and employees.
The benefits companies enjoy include the following:
- Documentation and paperwork can be simplified with this approach.
- It saves and optimizes the use of time, money, and human resources for a company.
- It ensures accountability across each department while assigning responsibility to personnel undertaking varied tasks across an organization.
The benefits employees enjoy include the following:
- Through a common platform and communication mechanism, data sharing is simple, and employees need not spend time approaching multiple people to secure the required information while completing their tasks.
- This system can boost job satisfaction among employees and offer opportunities for growth and development.
- Since every aspect of a job is planned, employees typically do not experience undue work pressure and anxiety.
Some of the benefits that the teams enjoy:
- Teams find collaboration easy with process centering.
- With well-defined processes, teams are equipped with the knowledge to perform, including formal access to clearly defined roles and responsibilities.
- Teams can concentrate on continuous improvement and Kaizen projects as workflows are planned and sequential.