Table of Contents
What Is Storage Cost?
Storage costs are the costs incurred for storing inventory. They can be direct or indirect and include rent, space, software, electricity bills, and warehouse personnel. These costs are part of the inventory value and vary according to the industry.
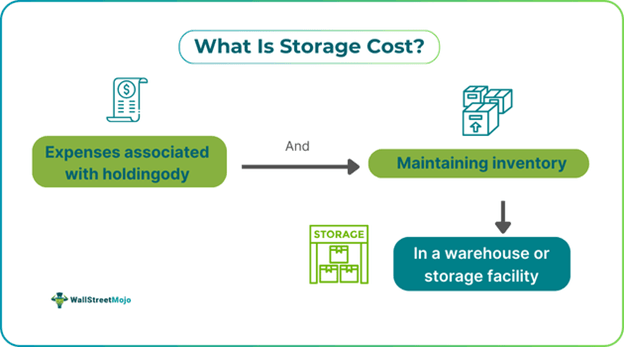
These expenses are also associated with inventory maintenance. They vary according to several factors, including the product quantity, type, location, and size of the storage unit. The length of storage time is also an influential factor in their determination. In addition, the cost incurred for additional inventory units does not increase at constant rates.
Key Takeaways
- Storage costs are expenses that are incurred in reference to maintenance and storage of inventory. They are, hence, a subset of inventory carrying costs.
- These include expenses such as electricity and utility bills, insurance, labor, maintenance, and equipment charges.
- They are likely to increase with the increase of variable costs. Facility costs, funding costs, mitigation costs, taxes, etc., influence the costs.
- Management of the costs is therefore crucial for business. It can be reduced by planning warehouse layout and automating certain sections.
Storage Cost of Inventory Explained
Storage costs are costs that are associated with expenses incurred with reference to the storage and maintenance of inventory. It is, hence, a subset of a business's inventory carrying cost. Inventory refers to the products or materials required to create the product that are in stock. Companies typically store the products in their storage facilities such as warehouses, and generally, they are located near the company premises or customers. However, some businesses may need that option, and the cost involved in maintaining a distant storage facility is also included in these costs.
They include rent, leases, electricity and utility bills, insurance, equipment charges, labor and other expenses. The costs of the associated things generally rise at an exponential rate and are often referred to as economies of scale. This is because even though the fixed costs, such as rent and utilities, may be lower, they tend to be high when spread over large areas. However, the cost involved per unit of storage may decrease as the inventory levels rise. This, too, may rise when the variable costs that are used to maintain increased inventory rise, such as maintenance charges and labor charges.
The costs involved in storage have to be carefully maintained as they can impact the competitiveness and profitability of the business. Storage can be carefully planned by laying out better warehouse storage designs, automating picking systems, managing inventory, etc. The first steps of management start with the location and the number of items stored. Hence, planning shall begin with the same.
How Is Storage Cost Distributed?
Storage costs can be distributed on the basis of many factors. Some of them are given as follows.
- Cost of facility: Warehouse running costs are carefully curated based on factors such as building area, value, depreciation, insurance, and utility expenses. They include the costs incurred for storing items and the safety measurements taken to safeguard them.
- Cost of funds: Businesses often borrow money to acquire inventory, which is also included in storage costs. Market rates can fluctuate often, impacting the cost of buying materials, transporting them, and storing them.
- Cost of risk mitigation: Inventory storages need a significantly damage-proof environment. This may include buying fire extinguishers and bubble wrap, hiring security personnel, etc.
- Taxes: Businesses are taxed on their income, and a share of the profit is paid as taxes. Companies anticipate these costs in the inventory and the sale price of the products.
- Other factors: Storage costs also include the total rental time, the amount of inventory, climate control options, and quality maintenance charges.
Examples
Let us look at some of the examples to understand the concept better.
Example #1
Suppose Dan is a small business owner who sells clothes. Due to a surge in demand, he needs additional storage space and purchases a small building to store his inventory. To determine his monthly storage cost, Dan decides to calculate it using a simple formula manually:
Storage costs = (Warehouse, electricity, and utilities costs) + (Material handling costs) + (Personnel costs) + (Climate control costs) + (Area in square feet × Locality cost per square foot)
He gathers the following data for his calculation:
- Warehouse, electricity, and utilities: $500
- Material handling: $200
- Personnel: $200
- Climate control (to protect clothes from moisture): $150
- Storage area: 1000 square feet, with a locality cost of $0.20 per square foot
Calculating the area cost: 1000 sq ft × $0.20 = $200
Now, adding all the components together: $500 (warehouse/utilities) + $200 (material handling) + $200 (personnel) + $150 (climate control) + $200 (area cost) = $1,250
Therefore, Dan's storage cost per month is $1,250.
Example #2
Costs associated with storage are rising due to a shortage in warehouse space, with rental rates exceeding $ 150 per square meter annually in Tashkent and Almaty. The demand is primarily driven by expanding trade along the Middle Corridor, connecting Asia and Europe. This shortage has led to a construction boom in warehousing, though concerns remain about potential oversupply. Additionally, infrastructure development, such as road improvements, needs to catch up to the rush to build, which could impact trade efficiency and broader economic conditions. This example highlights critical issues related to logistics and regional development.
Storage Cost Vs. Holding Cost Vs. Carrying Cost
The differences between the concepts are given as follows:
- Storage costs are those that are incurred as part of storing inventory. Carrying costs are those costs that are incurred as a result of holding and storing inventory. Holding costs are also costs associated with holding and storing inventory. However, these include the cost of unsold items.
- The cost of storage includes warehouse fees, insurance, and maintenance fees. It is a subset of carrying costs, which include storage fees, taxes, insurance, opportunity costs, and other related costs. Holding costs include storage costs, cost of capital and finance costs, insurance and taxes, obsolescence, and shrinkage costs.
- Costs incurred on storage can be calculated by using the formula: Storage costs = warehouse, electricity, and utilities cost + cost of material handling + personnel cost + climate control costs + (area in square feet * locality cost). Carrying costs are calculated using the formula carrying cost of inventory = (total holding costs of business inventory / total inventory value of the business) X 100. Holding costs are calculated using the formula: Inventory holding cost = storage cost + capital costs + obsolescence cost + insurance & taxes.