Table Of Contents
What is Conversion Cost?
Conversion cost is the cost incurred by any manufacturing entity in converting its raw material into finished goods capable of being sold in the market. It usually includes the total value of labor cost and other applied overheads like factory overheads, administrative overheads, etc.
Formula
Here,
- Manufacturing Overheads means the expenses directly attributed to each unit of product or the process. These include electricity bills, rent, depreciation, plant insurance, repairs and maintenance of plants, etc.
- Direct Labor is the direct cost associated with manufacturing the product, such as wages, salaries to workers, pension funds for workers, insurance of production staff, supervision, etc.
Conversion Cost Examples
Some examples of conversion cost are as follows -
- Machinery depreciation
- Plant and machinery maintenance
- Salary to production staff
- Direct labour benefits
- Rent of factory
- Utility bills
- Factory insurance
- Production supervision
- Salary of staff related to production
Let us take an example to understand this concept.
Samsung has a cell phone production unit with a production capacity of 10,000 daily it incurs day-to-day expenses to keep its business running. The company wants to know its conversion cost from the following mentioned information.
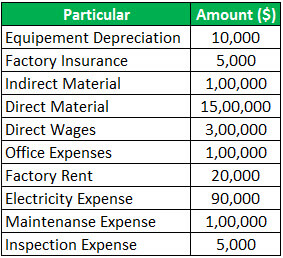
Solution:
Direct Labour = $3,00,000
Manufacturing Overheads = 10,000 (Equipment Depreciation) + 5,000 (Factory Insurance) + 80,000( Indirect Material) + 20,000(Factory Rent) + 90,000(Electricity expense) + 1,00,000(Maintenance expense) + 5,000(Inspection expense)
- Manufacturing Overheads = $3,10,000
- = $3,00,000 + $3,10,000
- Conversion Cost = $6,10,000
- = $6,10,000 / 10,000
- Conversion Cost per Unit = $610
Importance
- t is a measure used to allocate unallocated overhead costs to products manufactured for better cost planning and monitoring.
- It helps business to ascertain the cost of inventory which needs to be reported in the balance sheet as an asset.
- The proper application helps businesses to determine the selling price per unit, thereby achieving its profit margin.
- In the case of inefficiencies, it helps redesign and reengineer the production.
Conversion Cost vs Prime Cost
- Conversion cost and prime cost are both manufacturing sector terminology and are used to determine the effectiveness in the production of a particular product. Conversion cost can be defined as a costing terminology that provides information on indirect labor and overhead expenditure to convert basic raw materials into finished goods. At the same time, the prime cost is another costing term that quantifies the value of direct material, direct labor, and other direct expenses incurred in manufacturing any particular product.
- Both conversion and prime cost use many of the same production factors, but each has a different opinion on product efficiency. ยท Both conversion and prime cost use many of the same production factors, but each has a different opinion on product efficiency. Prime cost uses both direct material and labor to complete a product, while conversion cost does not include a direct material cost. Certain cost elements are included in one and excluded in another like prime cost does not include overhead expenses, which are applied in conversion cost. Prime cost is calculated and presented at the beginning of the cost sheet, but there is a standard that requires the calculation of conversion cost until and unless the manager desires it. The premium coast's main objective is to set a product's price with the desired profits. In contrast, the conversion cost is calculated to sum up and resolve any manufacturing inefficiency.
Advantages
- It helps to determine the amount spent in turning raw material into a product.
- It helps eradicate any deficiency in the production process and helps in reducing the cost of production.
- It helps managers to supervise and keep track of expenses of production.
- It is used in developing a price model for a product and estimating the cost of the final product.
- Managers and business owners sometimes use conversion costs to determine if any waste can be eliminated
- This is used to determine the cost of sales to report it on the financial statements (if applicable).
Disadvantages
- It does not give an idea about all the costs incurred in production/ manufacturing as it considers only two elements - direct labour and overheads.
- This concept is irrelevant in cases where the product does not undergo any conversion and can be sold directly with minimal processing.
- This concept cannot solely be relied on for cost control and reduction program as it does not cover all elements of cost. There are better costing mechanisms like marginal costing, process costing, etc. which provides better insights into the cost incurred.
Recommended Articles
This has been a guide. What conversion cost is & its Definition. Here we discuss its formula, calculations, and examples, along with its advantages and disadvantages. You can learn more about it from the following articles โ