Table Of Contents
What Is Item Master?
An item master refers to a record listing all the crucial details regarding a stock item. Product managers and people in different departments of a business utilize the information to determine when the production of a particular product took place, the cost incurred to manufacture it, and other vital information.
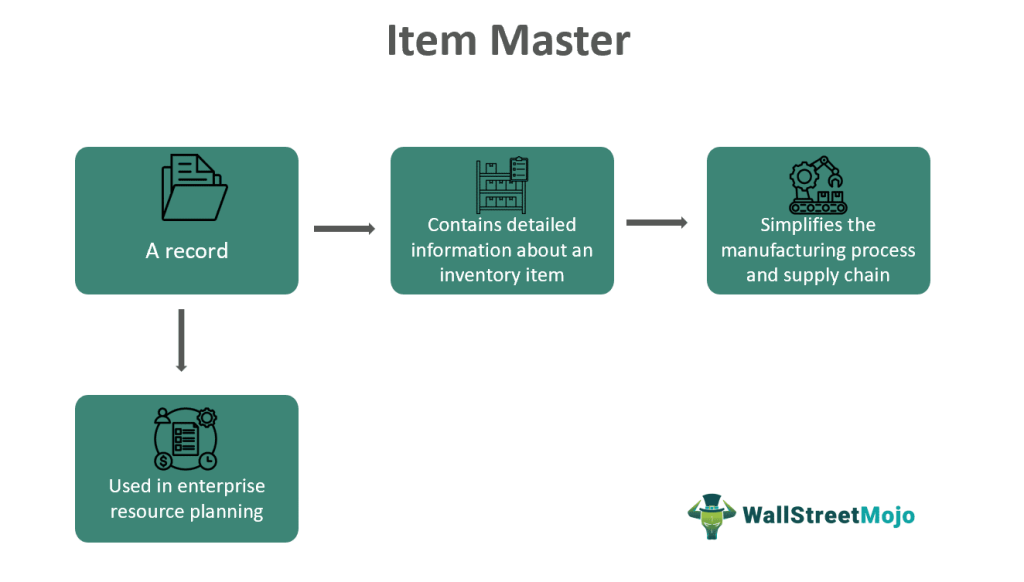
The details of an inventory item may include the unit of measure, description, ordering quantity dimensions, weights, etc. Thus, the record serves as a source of information for an extensive range of production planning and purchasing activities. For instance, a company may utilize the record to specify the weight dimensions of any product that they’ll order from a vendor.
Table of contents
- The Item master refers to a record that includes vital information related to a specific product in a company’s stock. This type of record helps certain people within an organization to know the cost of acquiring or manufacturing the product, when to start producing again, weight and dimensions, etc.
- A key benefit of an item master in ERP is that it allows companies to understand the changes in the cost of the product.
- Item master best practices include working backward from crucial decisions, developing a process, planning for data interconnectivity, etc.
Item Master Explained
The item master refers to an accumulation of all pertinent details relevant to certain products in an organization’s inventory. Typically, one can find such a record in a business’s enterprise resource planning (ERP) system. A key feature of these records is that they are comprehensive; they consist of every key detail that managers of different levels within the organization would require to make decisions related to the product.
Generally, the structure of an item master table includes the following components:
- Details of the supplier
- How much quantity is already present in the inventory
- The costs of the materials utilized
- List of the materials utilized to manufacture the product
- Name of the product
- Description of the product
- Where do the materials come from
- What quantity to order
- Time taken to manufacture
Note that the organization of the above information depends on how a business carries out operations. Also, the greater the information contained in any item master, the better an organization can optimize and enhance it gets on manufacturing, selling, and stocking of the product. Typically, such a record has at least the information listed above. That said, there might be more information that is specific to the particular product. Senior business leaders usually determine such custom information.
Examples
Let us look at a few item master examples to understand the concept better.
Example #1
Suppose in an item master of Company XYZ’s ERP, Product ABC is a smartphone. Its stock keeping unit or SKU is 002. The record consists of the following details:
- Screen size: 6.5 inches
- Random Access Memory: 8 GB
- Storage: 128 GB
- Cost of production: $100
- Product name: Venti XR
- Weight: 250 grams
- Materials required for production come from China
- Production time: 27 hours
- The production process starts again once the stock reaches 30 units.
Such details enable the organization to plan sales, raw materials purchases, and production in an efficient manner. Also, the information offers clarity regarding the production process.
Example #2
In October 2023, Intelliwave Technologies announced a strategic collaboration with CMiC. The latter has helped the former come up with a fully integrated solution. It will digitize construction accounting processes for material issuance, payments, and receiving.
The integration will benefit both organizations’ customers through project and item master creation. This is because it will be possible to seamlessly link projects to SiteSense from CMiC along with the individual or global configuration of the integration touch points. Moreover, all the records in the item master from CMiC will sync to SiteSense, populating part number records.
Best Practices
The item master best practices are as follows:
- Create A Process: Businesses must understand which fields or details are the most crucial for the item master in terms of analysis, inventory, and purchasing. Moreover, they must include those components in every such record as a standard. They can create a process document, which will eliminate the guesswork from the process of creating the record. This will ensure the efficiency of the production line.
- Develop A Standard Template: Companies can build a template for such a record. This template will allow the employees to enter data for any new inventory item with accuracy.
- Work Backward From Crucial Decisions: At the time of creating such a record, individuals in an organization generally decide which details are worth accumulating and which information is not useful. They must think well about which additional details can prove to be helpful in the future. In other words, when deciding, they must remember that tomorrow’s decisions will depend on data accumulated today.
- Plan For Interconnectivity Of Data: When a business accumulates information properly, such a record can offer a robust and powerful information source. That said, the data can be more valuable when the business combines them with other information, for example, accounting details and sales projections.
- Assign A Librarian For The Records: Businesses need to assign one or multiple master librarians to review each of such records, ensuring data quality. Moreover, they must see to it that all records are in line with the process document.
Importance
One can understand the importance of item master in ERP by going through the following points:
- It can assist in simplifying the supply chain as well as the production process.
- Such a record offers help regarding money management, goods production, and sales, allowing businesses to plan things more efficiently. Moreover, it enables manufacturers to order more products from suppliers while keeping sufficient quantity in stock.
- It assists businesses in spotting defects at the start of the production process and manufacturing top-quality products.
- This kind of record allows production managers and people from the purchase, sales, and finance departments to get an idea regarding the operational process.
- It helps determine the cost of a particular inventory item. Moreover, it also shows if the costs are increasing or decreasing and whether the organization is generating sufficient money.
Frequently Asked Questions (FAQs)
Typically, such records are not identical for every company. This is because when creating them, organizations include elements like time taken for production, weight and dimension, supplier name, etc., based on what is crucial for their operations and products.
This type of record can give businesses an idea regarding what quantity to order from suppliers and make production on a timely basis to fulfill customer demand. In addition, it can guarantee raw materials’ availability for production.
Such software helps in managing and organizing data typically included in such records. This makes it easier to utilize the information and improve business processes.
It is a process that involves maintaining comprehensive information associated with an inventory item. For that, one needs to make changes to existing fields, create new fields per requirement, edit or add vendor details, etc.
Recommended Articles
This has been a guide to what is Item Master. Here, we explain the topic in detail, including its examples, best practices, and importance. You can learn more about financing from the following articles –