Table Of Contents
Materials Handling Definition
Materials Handling refers to the integrated activities of planning, execution, and monitoring of the movement and storage of materials and finished goods within a supply chain. It includes transportation, storage, security, packaging, and inventory control. The primary objectives of materials handling are to boost efficiency, minimize damage, improve safety, and reduce costs.
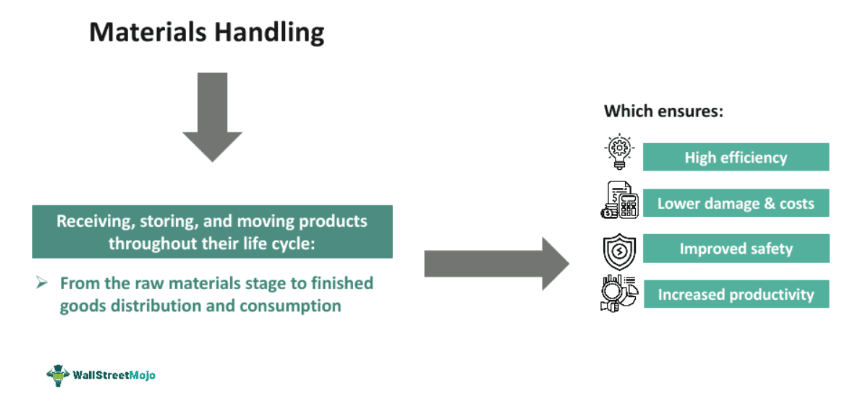
It forms part of supply chain management in many industries and is commonly practiced in warehouses, manufacturing units, and storage units. Effective materials handling plays a vital role in optimizing logistics and supply chain management through increased productivity, improved customer service, and enhanced overall sustainability of business operations.
Table of contents
- Materials handling is the short-distance movement of inventory, including raw materials and finished goods, from raw material receipt and consumption to distribution, including packaging, storage, and protection.
- Companies follow three main types or methods of handling materials. These are manual, mechanical, and automation-based materials handling.
- This function is of great importance across various, and effective assessment and operations can lead to reduced time and effort while maximizing productivity and profit.
- Materials handling equipment reduces manual effort, enhances overall productivity, and boosts operations safety. Machinery and technology in many forms are applied in industries with intensive material management requirements.
Materials Handling Explained
Materials handling involves moving items, finished and unfinished products, raw materials, and any other form of inventory within the manufacturing facility or across a group of buildings for different purposes like production, packaging, assessment, storage, or safekeeping. When companies undertake production activities, they need space to operate efficiently. Material handling systems play a vital role in establishing and managing a network of locations or areas for businesses.
These systems enable the efficient movement of materials from raw materials to finished goods across multiple locations, ensuring a seamless supply chain. Companies employ different material handling methods according to their production levels and capacities.
The nature of the goods or products they manufacture is also considered while making material handling decisions. The main goals of materials handling include effective inventory distribution at various points in the supply chain, efficient storage management, smooth production flow, and streamlined transportation for better operations results.
Material handling is an important part of operations. It is not just about moving materials from one location to another; it involves optimizing the entire process to achieve specific productivity and process rationalization goals. Only with a proper setup and planning can a firm achieve higher productivity, reduced costs, and increased efficiency.
By investing in the right equipment and technology, developing standardized procedures, and assigning material handling jobs to competent individuals, businesses can transform their operations into a competitive advantage that generates revenue for the company.
Principles
The following are the ten principles of materials handling.
- Planning: All aspects that contribute to materials handling should be planned well, and the performance, function, and objective must be properly defined from the beginning. A well-defined plan covers aspects such as layout & design, material flows, capacity planning, cost-benefit analysis, and contingency planning.
- Standardization: This principle describes the need for and importance of using standardized controls, tools, software, methods, machinery, and equipment. Flexibility, modularity, interchangeability, efficiency, and scalability are chief advantages of this process.
- Work: It focuses on minimizing the material handling activity and work without reducing productivity, hindering ongoing operations, and disturbing service levels. It also focuses on reducing waste.
- Ergonomics: This principle highlights the importance of designing systems that promote the physical and mental well-being of workers. It aims to reduce musculoskeletal strain, prevent injuries, and enhance overall safety and efficiency.
- Unit load: It states that products must be assigned proper weights and sizes to ensure efficient measurement, movement, storage, and transportation. It simplifies supply chain processes through better inventory control.
- Space utilization: This principle focuses on the effective utilization of the available space to increase productivity and process efficiency.
- System: It refers to integrating all the components and elements of the material handling process into a cohesive and well-structured system for optimization. It includes material flows, assembly, equipment & database systems selection, units & measurements, inspection, storage, production, order selection, packaging, transportation, and shipping.
- Environmental sustainability: This principle outlines the significance of building processes that do not adversely affect the environment. It covers energy consumption efficiency, sustainable packaging & warehousing, green transportation, and waste reduction, among other things.
- Automation: It states that automation and mechanization should be a company’s priority to make material handling more efficient. Automation improves consistency, responsiveness, and predictability and reduces manual labor, operational costs, and human errors.
- Life-cycle cost: Last but not least, this principle talks about controlling and optimizing the total cost of material handling equipment and technology, including machinery, tools, software, repairs, machinery disposal, etc.
Methods
Some methods of material handling have been discussed in this section.
- Manual material handling: This refers to using human labor for the movement of materials. Typically, labor is involved in activities like carrying, lifting, pushing, or pulling materials or equipment. Though manual handling is often the most cost-effective method, it can cause strain on the workers. Also, it is susceptible to human errors. Labor usually works with hand trucks, forklifts, pallet jacks, etc., while following manual systems. While it helps generate employment, it introduces operational challenges that may lead to losses.
- Mechanical material handling: This involves the use of machinery and equipment to move materials instead of labor. Forklifts, conveyor belts, cranes, and hoists are typically used to streamline work. Mechanical handling significantly improves efficiency and reduces the risk of bodily injuries. However, it requires a higher investment and demands routine maintenance and upkeep. Simply put, it replaces human labor with machinery and equipment within a warehouse or manufacturing facility. It is widely used across industries that deal with heavy and bulky materials.
- Automated material handling: It is an advanced form of material handling that uses robotics, Automated Guided Vehicles (AGVs), Automated Storage and Retrieval Systems (AS/RS), etc. These systems are customizable and can meet specific operational needs. They reduce the need for hazardous material handling processes. They also improve efficiency and productivity. However, implementing these systems is expensive.
- Hydraulic material handling: It involves the use of hydraulic fluids to power the movement of materials. For instance, hydraulic forklifts and cranes are popular. Hydraulic systems offer more power and greater precision, simplifying heavy-duty work.
Examples
Here are two examples of materials handling.
Example #1
Suppose Jennifer opens a chocolate factory and invests significant capital to buy a manufacturing plant. She buys raw materials in bulk, such as milk, syrup, sugar, etc. She hires 45 workers to ensure efficient operations. Each of them specializes in different tasks, and Jennifer divides them into groups to take care of material receipt, movement, production, packaging, storage, and shipment.
When suppliers deliver the raw materials, workers move them to the manufacturing unit. They carefully handle each task on the assembly line to ensure chocolates are ready for shipping. Once chocolates are packaged, the batches are moved to another unit of quality assessment, where weight and other parameters are verified. After the quality test, they are sent to the storage facility and carefully placed on shelves in line with certain safety guidelines.
When the distribution handlers arrive, the chocolates are moved from storage to distribution vehicles, such as trucks, and sent to the market. In this way, Jennifer plans the factory’s pre-production and post-production activities through effective handling and management of incoming and outgoing materials.
Example #2
A November 2023 report says that the global material handling equipment industry was valued at $216.6 billion in 2022. By 2030, the market is expected to reach around $342 billion, and the Compound Annual Growth Rate (CAGR) of 6% seems quite lucrative.
The report analyzes the changes taking place in this industry, including the advancements expected in the coming years. It includes applications, industries, types, and the study of top firms operating in this sector. SWOT analysis, competitive landscape assessment, and current market trend studies are part of the analysis. The factors responsible for growth have been given specific importance in this study.
The report further outlines how identifying and employing skilled labor is essential for the growth of this sector. It also states that skilled manpower has been a consistent problem for the industry. Due to this, many industries are taking suggestions for automation under advisement.
In addition, high investment requirements, location restrictions, and technology are other major concerns for the sector. For instance, the integration of Material Handling Equipment (MHE) has raised widespread concerns. To combat problems of labor and low productivity, companies have deployed specialized machines, industrial trucks, and cranes to increase their market share.
Importance
The importance of material handling has been discussed below.
- Material handling facilitates manufacturing, packaging, and storage since it is the primary activity of moving materials to initiate the said processes.
- In cases where it is a manual process performed by workers, it contributes to boosting employment in a given region.
- It streamlines the operations of manufacturing, warehousing, and facilities management companies. These industries have extensive material handling operations, and it plays a crucial role in ensuring that goods flow efficiently from raw inputs to the finished products stages.
- It steers operational improvements through innovation and technology. New machinery, automation, and software solutions are being developed regularly to enhance processes and boost company profits.
- Proper material handling facilitates the procurement, movement, storage, and safety of goods throughout the supply chain.
- With a well-thought-out material handling strategy, firms can reduce costs, increase productivity, and decrease effort and time spent on various processes.
Frequently Asked Questions (FAQs)
The common problems of materials handling are:
- A lack of diversity in storage materials
- Expensive automation and machinery
- A lack of skilled labor and experience
- Obstacles in finding the right location for warehouse setup
Material handling skills vary based on where workers are employed to work. For instance, manufacturing requires skills different from facilities management. Some basic skills include handling various tools and systems. Additionally, being able to operate material handling equipment, including software and heavy machinery, is a plus. Consistency and proficiency in meeting deadlines and completing the tasks assigned are important skills for effective overall control and inventory management.
The risks of materials handling are:
- Accidents and operational mishaps are possibilities. Hence, workers are asked to exercise caution.
- Incorrect movement and storage may result in damaged goods.
- Even short-term movements of materials or movement over negligible distances require companies to incur high costs since logistics is an expensive function.
- Improper facilities for storage and distribution of goods can result in financial losses.
- Inappropriate handling may affect product quality and lead to rejection in the market.
Recommended Articles
This article has been a guide to Materials Handling and its definition. We explain its principles, importance, methods, and examples. You may also find some useful articles here -