Table Of Contents
What Is Cycle Time?
Cycle Time refers to the amount of time (hours or days) a business takes to manufacture a particular product or provide a specific service. It is a critical factor in the manufacturing process, so keeping it under control is critical to the company's success.
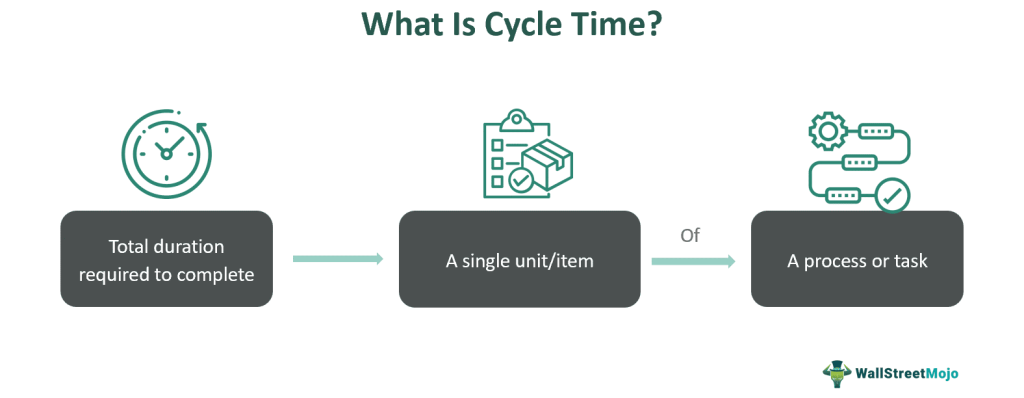
It is one of the most critical metrics to look at among a company's key performance indicators (KPIs). Reducing unnecessary time lag is critical for process improvement. This reduces both the cost and the manufacturing time. Proper timing of the manufacturing process results in quicker delivery and enhances the customer experience, eventually leading to higher profits.
Table of contents
- Cycle time definition states it as the amount of time (hours or days) a business takes to manufacture a product or provide a service.
- Enterprises use cycle time as a crucial indicator to assess the efficiency of all recurring processes.
- The procedure considers the amount of time firms need to produce the item and the wait periods between active work sessions.
- Time measurement and improvement can help businesses develop more quickly, outperform their competition, and retain talents. It serves as a crucial indicator of company success.
Cycle Time In Manufacturing Explained
Cycle time is the duration of a production process (of goods or services) from the start until the end. Usually, this time taken can be expressed in days and hours. This duration reveals the time between manufacturing and adding the product to the finished product inventory. These vary depending on the segments in the manufacturing sector, the size and location (globally) of the production facility, and the reliability of the supply chains that support the operation. It predicts the future of manufacturing as the metric quickly reflects improvements across systems and processes.
Enterprises use cycle time as a crucial indicator to assess the efficiency of all recurring processes. The procedure considers the amount of time businesses need to produce the item and the wait periods. The waiting period is the amount of time one leaves the item waiting on the board between active work sessions. This means that it captures operational tasks such as processing time and non-production time variables such as upstream, midstream, and downstream delays. The processing time includes inspection time for quality assurance and compliance. Capturing this information has its benefits.
A task becomes less efficient, the longer it takes to finish. The cycle duration measures efficiency identifies the areas of improvement and helps improve productivity by rectifying them. Efficiency and productivity increase as cycle duration decreases. They lower the cost per unit produced and reduce waiting times, which will let the products reach customers on time. Thus, customers will be happy, and profits will increase. It also strengthens the brand image of the company. Entities utilize the time saved through a correction in researching other innovations, which undoubtedly gives them an edge in the market competition.
Formula
This cycle time equation provides a precise measure of how to utilize the resources efficiently to generate output, aiding in the assessment and improvement of production processes.
Cycle time= Production Time / Output (number of units produced)
Production time in this context refers to the time utilized effectively. Subtracting wasted time from the total allocated active work time helps calculate this time.
Calculation Example
Suppose Dan, the owner of an electronics manufacturing company, aims to measure the time required to process an order. The factory operates for 8 hours a day, with
three breaks totaling 1 hour. Hence, the net production time is 7 hours per day. The workers can produce 100 units of products within this time frame.
Net production time per day = 8 hours - 1 hour = 7 hours
Total units produced per day = 100 units
Cycle Time = Net Production Time / Total Units Produced
= 7 hours / 100 units
= 0.07 hours per unit
Cycle Time vs Lead Time vs Takt Time
Understanding the differences between cycle time, lead time, and takt time is essential in optimizing production processes and meeting customer demands efficiently.
Key points | Cycle Time | Lead Time | Takt time |
---|---|---|---|
Meaning | It is the time it takes to create the product, measured in hours or days. | The lead time is known as the period between placing an order and delivery. | The average time that elapses between the start of manufacturing two subsequent product units is known as the takt time. |
Purpose | CT indicates the output rate. It is used to measure completion rates. | Lead time provides a broad picture of the sales and production processes. The arrival rate is computed using it. | Takt time is the pace at which companies must produce a product to keep up with customer demand. |
Formula used for calculation | CT = Net Production Time / Total Units Produced. | The lead time = The order delivery date - the order request date | Takt time = Available Production Time / total Units ordered (as per Customer demand) |
Cycle Time vs Throughput Time
Understanding the distinctions between cycle and throughput time is crucial for evaluating and optimizing production processes effectively.
Key points | Cycle Time | Throughput time |
---|---|---|
Meaning | The duration of a task from beginning to end is measured as CT. | The time taken by each procedure in the production process from beginning to end is measured by throughput. |
Purpose | CT, which measures the length of time involved from the beginning of the manufacturing process of a product until it is delivered to the client, is more frequently used to evaluate the overall responsiveness of laid-out plans. | Throughput analysis is commonly used to assess production performance because it makes it simpler to pinpoint the areas for improvement by segmenting the process into different parts. |
Formula | CT = Net Production Time / Total Units Produced. | Throughput efficiency rate = inventory/throughput time. |
Frequently Asked Questions (FAQs)
Increased profit margins for manufacturers result from producing more goods in less time. Reducing the length of the production cycle decreases labor costs, given the use of fewer raw materials, and fewer working hours of personnel. They are, therefore, a critical indicator of a business's efficiency and success.
Several factors can influence cycle time within a business's operations. These factors include the complexity of the production process, the efficiency of equipment and machinery, the skill level and availability of the workforce, the reliability of the supply chain, and the presence of any bottlenecks or inefficiencies in the production flow. Additionally, external factors such as market demand fluctuations and unforeseen disruptions can also impact cycle time. Identifying and addressing these factors is essential for optimizing cycle time and improving overall operational efficiency.
Reducing cycle time offers numerous benefits for businesses, including increased productivity, faster response to customer demands, improved efficiency in resource utilization, lower production costs, and enhanced competitiveness in the market. By streamlining processes and minimizing delays, businesses can optimize their workflows, deliver products and services more quickly, and maintain a competitive edge, ultimately leading to higher profitability and customer satisfaction.
Recommended Articles
This article has been a guide to what is Cycle Time. We compare it with lead, takt, and throughput time, and explain its formula, & calculation example. You may also find some useful articles here –