Table Of Contents
What is Blackflush Costing?
Backflush costing is a delayed accounting process used in a Just-in-Time (JIT) inventory system where the cost of producing goods and services like raw material cost, labor cost, and various other direct, indirect costs, overheads are determined, calculated, and recorded only after they have been produced, completed or sold by using a standard cost per unit multiplied by the number of goods produced.
Features
- In backflush costing, the cost of materials is not separately calculated but is transferred directly to the finished product account.
- Tracking work in the process is impossible, and no other work account is separately maintained.
- Journal entries in inventory accounts get delayed until the time of production or sale, and the standard costing mechanism is used to assign units when journal entries are passed.
- The cost of conversion is shared with the finished goods inventory account based on the operating time of labor.
- If the manufactured product involves not only one product but also many parts along with it with high or low variable consumption, backflush costing becomes inappropriate.
- When the units of goods are completed, the material cost is deducted from inventory, and finished goods are transferred to the material account.
How Does it Work?
By assigning a standard cost per unit of goods manufactured, the organization estimates the cost per material produced. Once the production cycle ends, the number of units manufactured is multiplied by the standard cost to evaluate the expense journal entry. This journal entry is recorded once at the end of the production cycle. Whenever an order is processed, only basic information is entered, including quantity, item number, and delivery date. Backflushing comes into play after the production process gets completed.
Example of Backflush Costing
ABC Inc., a Jute bag manufacturing company, has just started manufacturing business on 01/01/2020 and wishes to account for product costing. They have incurred various costs during January 2020 are as follows: –
- Direct material – “A” purchased on 05/01/2020 - $2,00,000
- Direct material – “C” purchased on 06/01/2020 - $1,00,000
- Direct labor for processing paid on 28/01/2020 - $3,00,000
The total units produced and sold during January is 60,000 units
Now, instead of recording each cost transaction, under backflush costing, ABC Inc. needs to pass a single accounting entry at the end of the period, which is: –
Expenses A/c Debited by $6,00,000 and bank A/c credited (assuming paid via bank)
Journal Entry of Backflush Costing
Entries passed are as follows: –
- Simple entry is passed by debiting expenses accounts and crediting payment a/c, i.e., bank or cash A/c or creditor A/c when purchased on credit.
- Finished Goods A/c is debited with all costs incurred in point 1. With corresponding credit above Cost A/cs like Direct Material Cost, processing cost (labor), etc.
- At the time of sales, the cost of corresponding goods sold is transferred to the cost of goods Sold with credit to Finished goods A/c.
When is Backflush Costing Used?
It is generally used by those companies which maintain a low inventory holding period and a high turnover in inventory Companies that experience slow turnover in inventory; they record the cost as and when they are incurred since the product may not be sold for a longer duration and may lead to incorrect inventory/ cost records.
It works well in the business process where huge costs are incurred in the production process of goods as it simplifies the accounting process in that case. Accordingly, companies with complex production processes opt for the backflush costing method. On the other hand, companies that sell more customized products do not opt for such costs as the cost per unit of goods varies with the product manufactured.
Backflush Costing vs. Conventional Costing
There are major differences in both types of costing methods. Under the conventional costing method, the entry for raw materials goes into the raw material inventory and then transferred to work in process inventory (WIP) and then to finished goods A/c. Under the backflush costing method, raw materials are ordered only when required, and they are accounted for. Under the conventional costing method, labor and overhead are charged directly into WIP; then, they are moved to sequential processing, finished goods, and later to the costs of goods sold. In the backflush costing method, these charges are directed into finished goods inventory or costs of goods sold.
Benefits
- Simplified accounting process as only a single journal entry needs to be made when the backflush costing method is used at the end of the production process, which makes it an easier choice.
- It allows companies to assign costs to correspond to inventory easily.
- It saves time for the companies to record every data during the production process, saving the accounting cost.
- It simplifies the bookkeeping process and administrative duties without losing much detailed information.
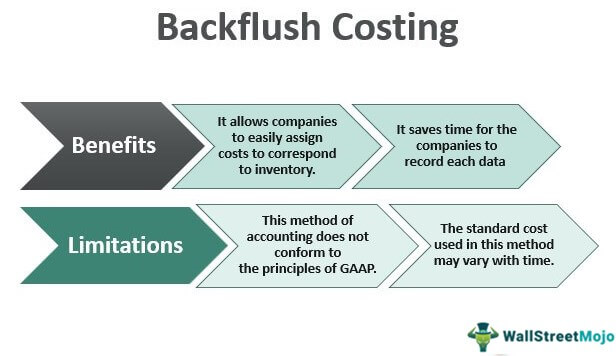
Limitations
- It is not useful for companies with slow inventory turnover as the recorded cost will be too long after it is incurred.
- This method of accounting does not conform to the principles of GAAP and therefore is not ideal for use always.
- The standard cost used in this method may vary with time and thus does not provide accurate accounting entries in the future.
- It is not useful for the businesses of the customized product as it would require the creation of an outstanding bill for each product, making it cumbersome.
Conclusion
The backflush costing method is a simplified method of recording expenses incurred in manufacturing products where all costs incurred are accounted for after some time of their incurrence. This can be used in a hybrid system where multiple methods of production accounting are used. It may not be suitable for an organization with a long production process but may prove a theoretically elegant process for complex accounting solutions.
Recommended Articles
This has been a guide to what Backflush Costing is. Here, we discuss features, examples, journal entries, and its benefits and limitations. You may learn more about financing from the following articles –