Table Of Contents
What is a Standard Cost?
Standard cost is an estimated cost determined by the company for the production of the goods and services or operating under normal circumstances and is derived by the company from the historical analysis of the data or from the time and the motion studies. Such costs pre-determined by the company are used as the target costs by the company for comparing it with actual costs, and the difference will be the variance.
The variance derived is then used by the company's management for knowing and correcting the cause, making a further estimation for the coming years, and decision making related to business. It almost always varies from the actual costs because the situation keeps changing, involving different unpredictable factors. Therefore, it is also known as the normal cost.
Components
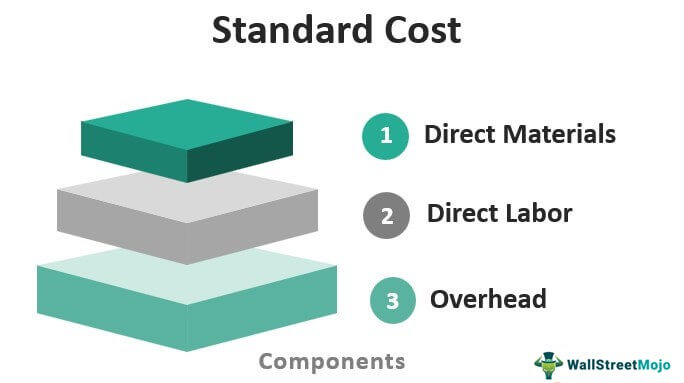
In manufacturing setup, there are three main components which include the following:
- Direct Materials - It is derived by multiplying the quantity of each material with the per-unit material cost.
- Direct Labor - It is derived by multiplying the quantity of each labor with the per hour labor cost.
- Overhead includes fixed overhead cost and variable overhead, calculated by multiplying standard quantity with the standard rate of variable overhead.
Example of Standard Cost
There is a company manufacturing watches. At the beginning of the year, the company calculated the cost of the production of the watches by considering the past trends and the expected future conditions of the market. In the coming year, the company will likely produce 5,000 units of watches.
Also, it is expected that the standard direct material cost per unit will be $100, the standard labor cost per hour will be $ 20, the standard variable overhead cost is $15 per hour, and the standard fixed cost is $100,000. Therefore, the total hours required for producing one unit is 10 hours. Find the standard cost of the company.
Solution
- Expected No of Production: 5,000
- Standard Direct Material Cost Per Unit: $100
- Standard Labor Material Cost Per Unit: $20
- Standard Variable Overhead Cost: $15
- Expected Total hours per unit: 10
- Standard Fixed Cost: $100,000
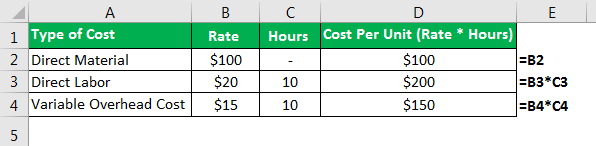
Total will be -
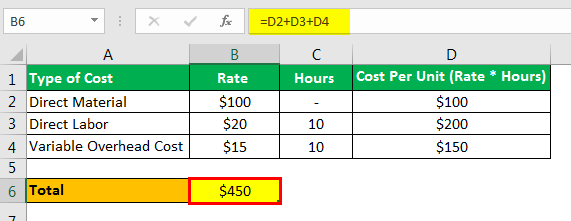
- Total = $450
The total Standard Cost will be
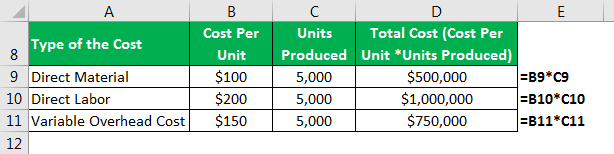
The total cost will be –
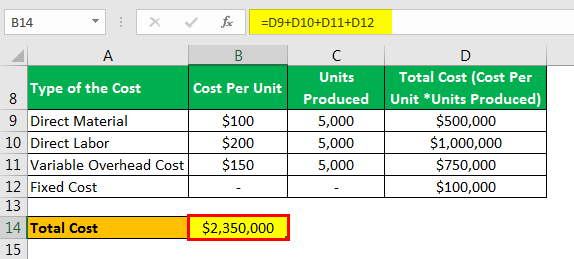
- Total Cost is $ 2,350,000
Advantages
- The company's management uses these costs to plan the process of future production and ways to increase the company's efficiencies.
- As the standard cost is calculated using the different statistical measures and the experiences of the management, so with the help of this measure, management can innovate new ways to produce the products that do not require the same type of procedures, thereby reducing the cost of the company.
- The management uses it to determine the reasonability of the actual costs of the period. The difference between the standard and the actual cost helps the management know-how close to actual expenses matched with what is expected and decide the future course of action. For example, if the actual cost of the material is much higher, then the management may investigate the reason for the excess cost.
Limitations
- Setting such a cost of production is difficult as it requires a high degree of technical skill from the person responsible for setting the same. Therefore it requires lots of effort and cost. Also, the conditions in any business enterprise keep on charging due to which standards have to be revised only on a timely basis; otherwise, it will not be worth anymore.
- The situations that would prevail in the future in any company or industry are not certain. Different factors affect the company, making it challenging to make the correct estimation of the standard cost of the production of goods or the provision of the services by a company. While calculating such costs, past experiences and future expense forecasts are required.
- It is impossible to fix these costs in every type of operation as such a system cannot be used in industries with no production of any of the standard products.
Important Points
- It almost always varies from the actual costs because the situation keeps changing, involving different unpredictable factors. The differences arrived are known as the cost variances.
- In case the actual cost of the company is higher than the standard cost, then the company has an unfavorable variance. In contrast, if the actual cost is less than the standard cost, the company has a favorable variance. The variances so arrived help the management evaluate the reason for variances so that appropriate actions could be taken.
Conclusion
It is the cost estimated by the company that normally occurs during the production of the goods or services, i.e., the amount the company expects to spend on the production. The management uses it to plan the process of future output, ways to increase efficiencies and determine the reasonability of the actual costs of the period. However, setting the standard cost of production is difficult as it requires a high degree of technical skill and the efforts of the person responsible for setting the same.
Recommended Articles
This article has guided what standard cost is and its definition. Here we discuss examples to calculate the standard cost in accounting along with advantages, disadvantages, and limitations. You can learn more about finance from the following articles –