Table Of Contents
Cost of Quality Definition
Cost of Quality can be termed as the process that measures and determines where and how organizations' resources are utilized to maintain quality and prevent poor outputs. It can be regarded as a method of process improvement and quality assurance and prevents internal and external audit failures.
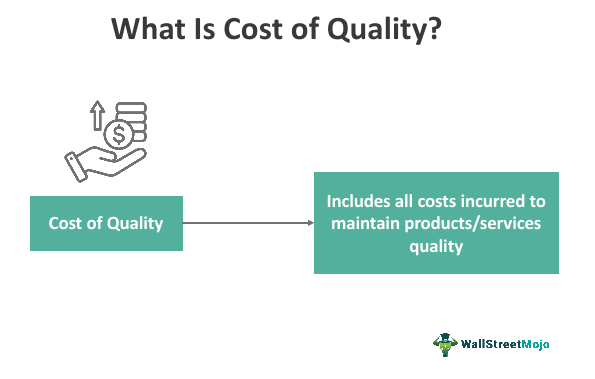
Incurring this cost is, of course, important as when firms spend on improving the quality of products and services, it helps them enhance their brand name in the market. However, keeping this expense of maintaining quality assessment tools active controlled without compromising on the product quality is also a great attempt. This is because in such a scenario, the amount saved is yet again used to improve the quality of the products.
Cost of Quality Explained
The cost of quality model signifies the costs the business has to bear to utilize its resources to maintain qualitative outputs to its targeted customers. If the business does not employ its resources to adhere to quality metrics, it will lose out on its competitive advantage. Furthermore, if the cost of quality is not incorporated, it can severely impact the business’s bottom line.
It discusses the organization's costs while trying to achieve and maintain quality output. The companies determine the cost of quality to derive a competitive advantage in the industry. By investing a fixed amount towards this cost, the business ensures that the failures are reduced and defects are eliminated.
The quality cost ensures that the business maintains a positive bottom line. If the company does not incorporate this cost, the business can incur high failure costs in the form of product returns and warranty costs, which can, in turn, dampen the bottom line altogether.
Types
There are four broad components: prevention costs, internal failure costs, external failure costs, and appraisal costs.
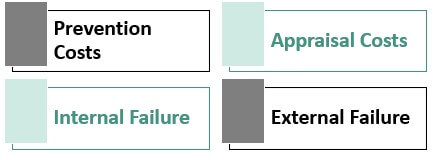
#1 - Prevention Costs
The prevention costs can be regarded as the costs the business incurs to reduce and minimize defects. The prevention costs are determined at the start of every new process step. The prevention costs are highly regarded as saving organized labor and manufacturing costs. If the business does not undertake the prevention costs, it could result in high defect costs at a later stage, which could prove to be expensive for the business.
#2 - Appraisal Costs
The appraisal costs can be regarded as the costs that the business incurs when it works towards identifying defective items. It is done before any product has to be shipped to the end consumer. The quality checks professional inspect finished goods in the process inventory and raw materials.
#3 - Internal Failure
Internal failure costs are the cost that the business or corporate entity has to bear once the defective items are identified before proceeding with the shipment. These costs signify the direct material, manufacturing overhead, and direct labor consumed by each defective item.
#4 - External Failure
The external failure costs are costs the business has to bear on account of defective items shipped to the customers. These costs are often regarded as expensive as they would cause the business to incur high warranty and return costs along with already incurred manufacturing overheads.
Formula
The mathematical expression to help one learn about how to calculate cost of quality is:
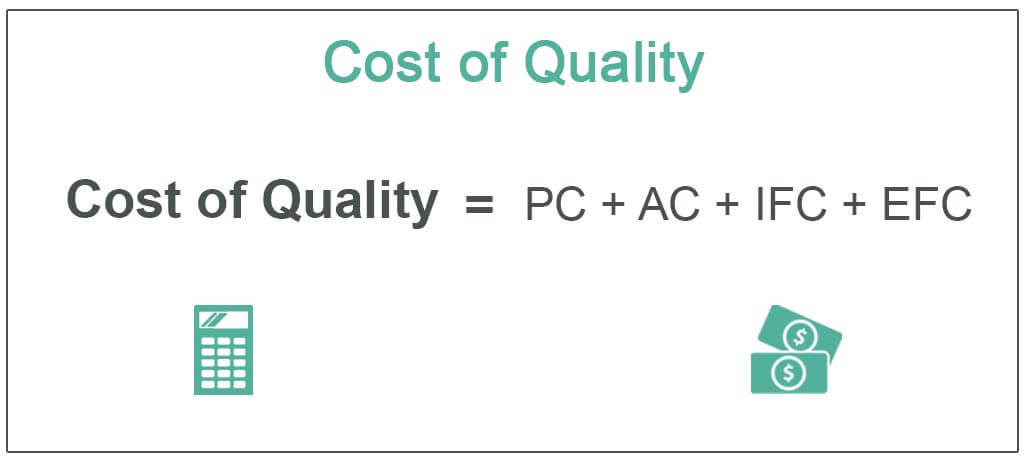
It can further be expressed as displayed below: –
Here,
- The cost of good quality is represented as CoGQ.
- The cost of poor quality is represented as CoPQ.
- The prevention cost is represented as a PC.
- AC represents the appraisal costs;
- IFC represents the internal failure costs.
- EFC represents the external failure costs.
Examples
Let us consider the following instances to understand what is cost of quality and also learn how to calculate it:
Example #1
Let us take the example of a business that generates $1,000,000 in sales. It incurs $10,200 in Quality checks and inspections. It pays $30,000 for appraising the purchased raw materials. Additionally, it pays $15,000 for repairs on finished items. It maintains a provision of $5,000 for warranty costs and product returns. Help the management determine the cost of quality as a percentage of sales.
Solution:
Step 1: Calculation of Total CoGQ
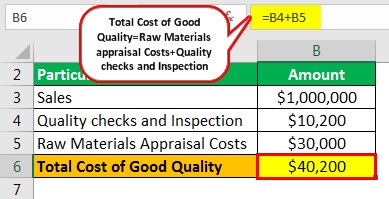
=$10200+$30000
=$40200
Step 2: Calculation of Total CoPQ
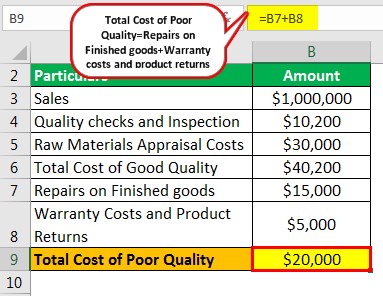
=$15000+$5000
=$20000
Step 3: Calculation of Total CoQ
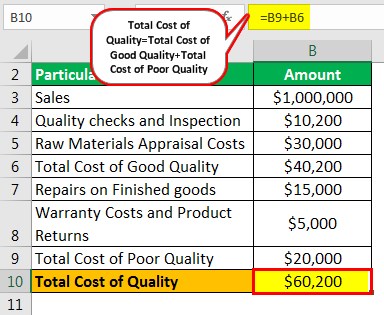
=$20000+$40200
=$60200
Step 4: Calculation of cost of quality as the percentage of sales
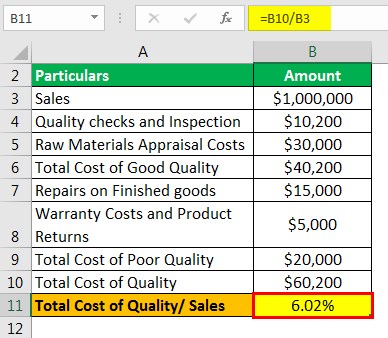
=$60200/$1000000
=6.02%
The inspection checks and appraisal costs on raw materials account for the CoGQ. The costs of repairs, warranty, and product returns account for the CoPQ.
Example #2
In June 2023, John Hopkins researchers published a report on The Volume and Cost of Quality Metric Reporting whereby they noted that the hospital used major resources for quality reporting and the tools and methods used to assess the quality of the systems and resources in the hospital are quite expensive.
The researchers, however, inferred that reducing the number of metrics for quality assessment should be considered by hospital authorities and they must take shifting to electronics metrics seriously. Overall, it was suggested through the report that the hospital must optimize resources for providing better services than quality assessment.
How To Reduce?
The cost incurred in maintaining the cost of quality is significant. As a result, firms or entities often think o implementing ways to reduce this expense. However, reduction in the quality cost is not about compromising with the product or service quality.
There are multiple ways in which the quality cost can be reduced. Some of them include:
- Identifying the systemic issues beforehand and take early corrective measures so that not much expense is made to deal with it at a later stage.
- In case entities plan to implement a change, they must consider change management tools to understand the repercussions of bringing about that change. These tools help figure out if the transition would be smooth or involve rough transformation for which the entities may have to remain prepared beforehand.
- Identifying operational errors and making sure they do not occur at a later stage. This is because such errors involve huge damage control cost, thereby making it a huge expense for the firms. Conducting training programs help entities have professionals who can identify and prevent such errors.
- Implementing various risk management techniques to avoid errors at advanced stages. To achieve this, the entities can ensure thorough audit management, proper financial reporting, and compliance with regulatory requirements.
- Enhancing or setting standards for suppliers’ quality is an essential step that one may take to reduce quality costs. Specifying benchmark performance and enhancing communication with the supplier is a must to make sure they are providing standard quality supplies based on the quality standards that a firm ensures for its finished products.
Importance
The determination of the cost of quality remains to be critical and varies for different organizations. If this cost is not measured and quantified, the organizations working in the competitive industries would never gain the upper hand and survive the ever-changing dynamic environment. Therefore, measuring it is necessary as it helps the business maintain a healthy and positive bottom line.
It is a fundamental methodology as it allows the business to derive a competitive edge over its peers working in the industry. These costs ensure that problems and root causes that can impact the business are identified very early, and preventive actions can be undertaken.
It also helps the organization devise and determine the corrective actions for any potential failures. It usually happens when an organization identifies defective products before and after shipping to the customers.
Benefits
The cost of quality helps the business derive a competitive edge over its peers working in the industry. It allows the organization to plan for costs that the business has to incur in maintaining quality costs and helps the organization make provisions over them, which helps the organization maintain a favorable bottom line.
Some of the advantages of incurring the cost of quality include:
- It helps the organization to chalk out wrong and poor-quality output.
- It helps in problem-solving, wherein it performs cost and benefits analysis on quality and process improvement initiatives.
- The model or cost of quality helps in a single-point evaluation of quality performance.
- It further evaluates the costs of failures and appraises them accordingly.
Cost of Quality vs Cost of Poor Quality (COPQ)
Cost of quality and cost of poor quality are two terms that are often used interchangeably, but then they share a considerable number of differences.
Let us have a look at the distinction between the two below:
- The cost of poor quality (CoPQ) is a subset of the cost of quality.
- The CoPQ is the business cost incurred when the defective products are identified before and after shipping to customers.
- Therefore, the sum of internal and external failure costs can be termed the CoPQ.
- The CoPQ usually consists of product return costs and warranty costs related to the products.
- On the other hand, the cost of quality is determined by the CoGQ and CoPQ.
- It is determined as the sum of the cost of good quality and poor quality.
- The cost of quality takes into account prevention costs, appraisal costs, internal failure costs, and external failure costs.
- The prevention and appraisal costs do not constitute the CoPQ as such costs attempt to identify defective products at the beginning of the production process.
- The CoPQ arises after the end of the production process and on defective finished goods.
Recommended Articles
This article has been a guide to Cost of Quality and its Definition. We explain it with examples, types, formula, importance, benefits, how to reduce it, and vs COPQ. You can learn more about financial analysis from the following articles –