Table of Contents
Lean Operations Definition
Lean operations are like running a business on a tight budget. It's all about doing a lot with a little. This strategy focuses on simplifying things and finding ways to improve every aspect of the business every day. It helps businesses run smoothly and get better at what they do.
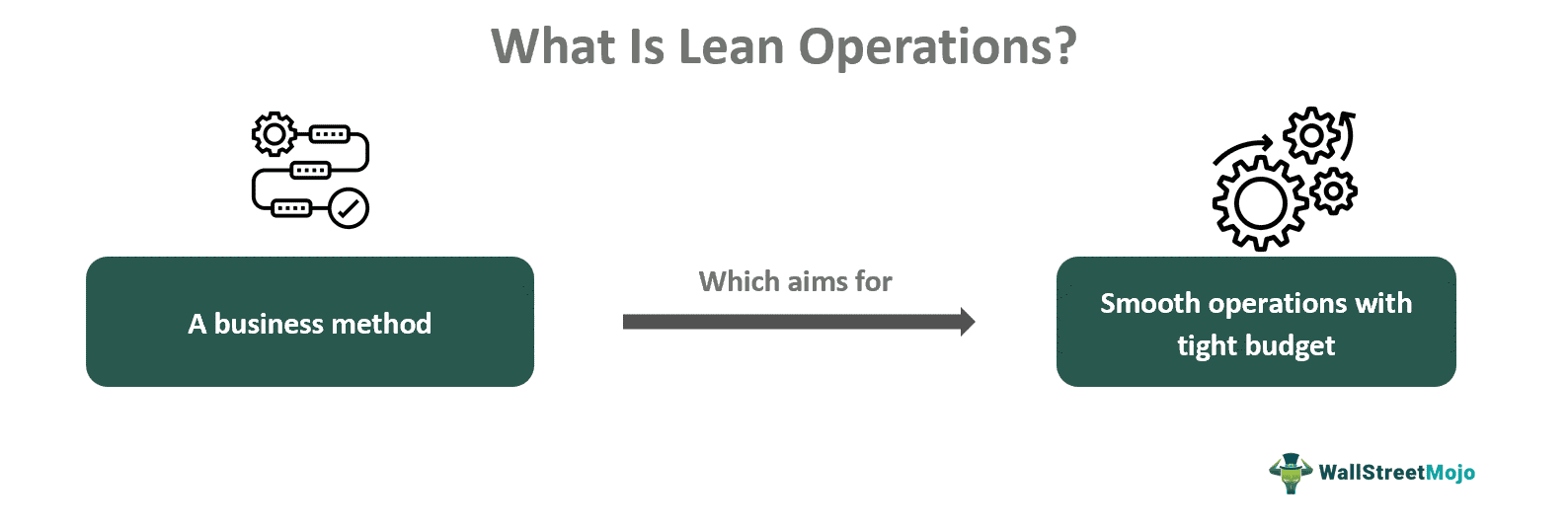
It brings numerous benefits by making organizations more efficient. Those who apply lean principles believe that the market determines prices. They prioritize meeting customer needs, ensuring satisfaction, simplifying production, and staying cost-effective.
Key Takeaways
- Lean operations focus on maximizing efficiency and minimizing waste in business processes.
- It involves streamlining operations, eliminating unnecessary steps, and optimizing resources to deliver value to customers while reducing costs.
- Lean principles encompass continuous improvement, respect for people, value stream mapping, and pull-based processing.
- Lean operations are vital for businesses, reducing costs, boosting productivity, and enhancing customer satisfaction.
- By eliminating waste and maximizing value, they ensure efficient operations and sustainable growth, aligning with organizational goals and enhancing competitiveness in the market.
Leading By Example Explained
Lean operations is a method that aims to make businesses run smoother and save money. It started with Toyota in the 1930s, but now, lots of other companies use it, such as hospitals and builders. The main idea is to give customers what they want while saving money. This means constantly finding ways to do things better and faster.
Running a business is tough, and owners are always looking for ways to make it better. Lean operations tools and principles are a great way to do that. It's all about getting the most out of what you have, like time and resources. This helps cut costs and make things more efficient. Plus, customers are happier when things run smoothly.
Lean operations tools are essential for businesses. They help save money, get more done, and keep customers happy. By constantly looking for ways to improve, businesses can stay ahead of the game. It's like constantly fine-tuning a machine to make it work perfectly.
Characteristics
The characteristics of lean operations are as follows -
- Saving Labor Effort and Time: It focuses on using employee time and effort efficiently. Training programs are essential to teaching everyone in the company how to apply Lean principles to their work. This ensures that every employee understands their role in making processes more efficient.
- Eliminating Overproduction: Overproduction can be costly for a business because it leads to excess inventory that may not be sold. It advocates for producing goods only as needed, based on customer demand. This requires close coordination between sales, marketing, and production teams to ensure that production aligns with market needs.
- Optimization of Space: It emphasizes using the workspace efficiently. This means getting rid of any unused or unnecessary space that doesn't contribute to productivity. The focus is on prioritizing resources for producing goods rather than maintaining lavish work environments.
- Reduction in Defects: Defects in products can disrupt operations and increase costs due to rework and delays. These operations prioritize identifying and fixing defects quickly to minimize disruptions in the supply chain. This involves emphasizing quality control measures and addressing issues promptly to ensure smooth operations.
Principles
In a lean operations system, there are key principles that organizations follow to achieve efficiency without incurring extra costs.
- Keep Getting Better: They believe in constantly improving. By making small changes over time, they cut waste and work better. For example, a factory might find ways to make things faster.
- Value Everyone: They treat their employees well because happy workers do better work. They might reward employees who come up with good ideas.
- See the Whole Picture: They look at every step of a process to find where things go wrong. This helps them get rid of waste and work smarter. For example, a hospital might look at every step of how patients are seen to make things faster.
- Go with the Flow: They make things based on what customers want, not what they think they want. This stops them from making too much stuff that no one buys. For example, a café might only make sandwiches when customers ask for them instead of making lots and throwing them away.
Examples
Let us look at some examples to understand the concept better -
Example #1
Let's say there's a small bakery called "Fresh Bites Bakery" that wants to implement these operations to improve efficiency.
To start, the bakery decides to streamline its production process. They notice that they often have leftover bread at the end of the day, leading to waste. So, they implement a pull-based processing system where they only bake bread based on customer demand. This helps them avoid overproduction and reduce waste.
Next, the bakery focuses on optimizing space. They rearrange their kitchen layout to minimize unnecessary movement and maximize workspace efficiency. It allows bakers to work more smoothly and quickly without bumping into each other or wasting time searching for tools.
Then, they introduce continuous improvement practices. Every week, the bakery team meets to discuss any issues or inefficiencies they encounter and brainstorm solutions. They make minor adjustments to their processes, like adjusting baking times or reorganizing ingredient storage, to constantly improve their operations.
As a result of these operations initiatives, Fresh Bites Bakery sees a reduction in waste, an increase in productivity, and happier customers who enjoy freshly baked bread every time they visit.
Example #2
In the complex landscape of government contracting, King Aerospace shines as a beacon of efficiency and service excellence. Through the meticulous implementation of such operations, the company continuously refines its processes to eliminate waste and optimize resource utilization. This strategic approach not only drives cost savings but also enhances the overall value proposition offered to government agencies.
Moreover, King Aerospace's unwavering commitment to service is deeply ingrained in its corporate culture. With a workforce comprising over a third of individuals with military backgrounds, the company embraces a sense of duty and patriotism in serving its nation. This ethos permeates every aspect of its operations, fostering a collaborative environment where employees are empowered to deliver exceptional results.
Beyond the bottom line, King Aerospace prioritizes customer satisfaction as a cornerstone of its business philosophy. By maintaining streamlined communication channels and a relentless focus on meeting client needs, the company consistently exceeds expectations. It solidifies its reputation as a trusted partner in the government contracting space.
Importance
- Reducing Costs: These operations are akin to a meticulous accountant identifying and eliminating unnecessary expenditures. By scrutinizing processes and eliminating waste, businesses can significantly trim costs and bolster their bottom line. For example, a manufacturing company employing lean principles might uncover excess production leading to overstock and adjust operations accordingly, reducing unnecessary expenses.
- Increasing Productivity: It acts as a finely tuned engine, optimizing each component to enhance overall performance. By streamlining processes and minimizing non-value-adding activities, businesses can amplify productivity. For instance, by reorganizing workflow and eliminating bottlenecks, a company can expedite production, allowing employees to accomplish more tasks efficiently.
- Improving Customer Satisfaction: Such operations serve as a beacon guiding businesses toward delivering unparalleled customer experiences. By aligning operations with customer expectations and removing obstacles to satisfaction, businesses can cultivate lasting loyalty. For example, by shortening lead times and improving service quality, a company can ensure prompt delivery and exceed customer expectations, leading to enhanced satisfaction and loyalty.