Table Of Contents
What is An Inventory Audit?
Inventory Audit refers to the checking of the methods that companies use to record the inventory. It involves different analytical procedures to ensure that the proper record of the inventory is maintained in the book of accounts of the company and the same matches with the physical inventory count available.
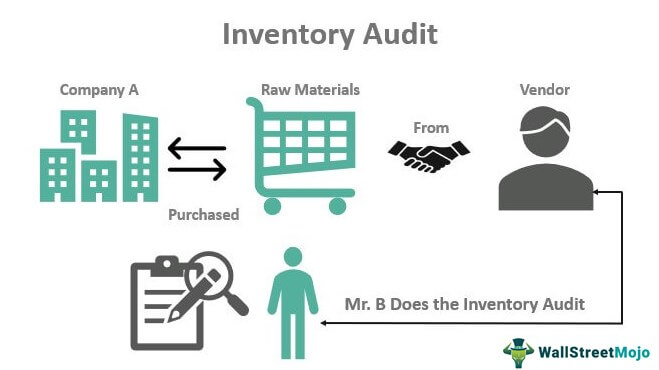
The process helps maintain the accuracy of the inventory, helps find the spot causes of the shrinkage in the inventory, if any exists, and helps ensure that there is the availability of the right amount of stock in the company at the right time. However, the big concern is that inventory audits occur frequently, and such a detailed audit will increase the company’s cost.
Table of contents
- An inventory audit is a type of audit that is performed to verify the accuracy and completeness of a company's inventory records.
- The audit typically involves physically counting inventory items and comparing the results to the inventory records maintained by the company to identify any discrepancies.
- An inventory audit helps ensure that the company's inventory records are accurate, that inventory is properly valued, and that the company is adhering to relevant accounting standards and regulations.
- It also assures stakeholders of the reliability of the company's inventory-related financial information.
Inventory Audit Explained
An inventory audit program helps tally a company’s finance against the officially recorded inventory to make sure the count matches the physical inventory.
It is the process in which the appointed auditors adopt different analytical procedures to verify the inventory methods used in the company for recording the inventory.
Through this auditing, the auditor conducts the counting of the physical inventory where all the types of inventories available in the company are counted and are then matched and reconciled with the inventory count available in the company’s books of accounts.
Objectives
To understand the inventory audit meaning better, it is important to be aware of the purpose behind conducting it:
- In the inventory audit, different analytical procedures are used by the auditor appointed to check the inventory methods used in the company for recording the inventory. It helps in maintaining the accuracy of the inventory.
- With the help of the inventory audit, the company may be able to find the spot causes of the shrinkage in the inventory if any exists. After identifying the reasons, the company may take corrective actions and can avoid the same in the future.
- Along with checking the inventory methods used by the company, an inventory audit helps ensure that there is the availability of the right amount of stock in the company at the right time. Because if there is extra stock then needed, it will lead to loss of opportunity cost, and on the other side, if there is a lack of availability of stock, later it would hamper the production of the goods. So any business needs to ensure that there is the right amount of stock in the company at the right time.
Procedures
To know how to do an inventory audit, one must be aware of the multiple procedures to consider:
Physical Count
In this method, the inventory in the warehouse is counted manually. The figures obtained are matched with the numbers recorded in the system. It might be a time-consuming process, but reliable enough.
Cut-off Analysis
This is the procedure where the shipment and receipt of finished products are put on hold until the counting and crosschecking of the inventory are complete. This is done to avoid confusion and keep track of uncontrolled variables in a particular financial period.
Freight Cost Analysis
This involves the cost incurred in transporting items from one place to another. Hence, this analysis takes into account the products lost or damaged during transportation.
Overhead Analysis
This is the inventory audit procedure in which direct material and labor expenses are excluded. Figuring out this number allows companies to assess the effect of overheads on inventory costs, which, in turn, lets them plan their budget accordingly.
Finished Goods Inventory Analysis
Adopting this process enables companies to assess the inventory costs used to manufacture and make finished products. As a result, businesses can check the inventory value of the finished goods to tally the financial statements.
Example
Let us consider the following inventory audit example to understand the concept well:
Company A Ltd purchases the raw material from the vendor, processes it and converts it into the finished goods. Then, it appoints Mr. B to conduct the inventory audit.
Mr. B follows different procedures to complete the audit. First, he counts the physical inventory, where he includes every piece of the inventory. Then, he matches and reconciles the inventory count available in the company's books of accounts and cut-off analysis.
Consistency of charging the freight cost in all the periods, either as an expense or included in the inventory cost. Conducting the direct labor cost analysis, overhead cost analysis, testing the work in progress, analyzing the cost of the finished goods; inventory allowances in case of the obsolete inventory, testing that the inventory is valued as per the method required by the law, etc.
Checklist
The vital points to consider while cross-checking inventory are as follows:
- It is of particular importance in manufacturing companies because they have raw materials to convert into finished goods. A proper inventory audit in place in such companies helps maintain healthy business practices related to the inventory.
- In the inventory audit, different analytical procedures are used by the auditor appointed to check the inventory methods used in the company for recording the inventory. It helps maintain accuracy and find the spot causes of inventory shrinkage. After identifying the causes, the company may take corrective actions and avoid the same in the future.
- A business needs to ensure the availability of the right amount of stock in the company at the right time. Using the inventory audit, a company can ensure it. If extra stock is needed, it will lead to a loss of opportunity cost. On the other side, if there is a lack of stock availability, it would hamper the production of the goods.
- If the concerned person has a good understanding of the stock flow in the company, then it helps ensure that the work of the company runs smoothly, as one knows the availability of the stock and its requirements in the future.
Risks
The disadvantages related to the inventory audit are as follows:
- The big concern, inventory audits take place very frequently. Such a detailed audit will increase the cost. To reduce the cost, the auditor has to limit his auditing scope and resort to techniques like test checking, etc.
- As there is the involvement of humans, there are chances of manipulation. Sometimes auditors manipulate the data and show a different position. In those cases, the inventory audit will not give fruitful results.
Frequently Asked Questions (FAQs)
The optimal frequency of inventory audits depends on various factors, such as the inventory size, industry regulations, internal control processes, and the organization's risk tolerance. Generally, companies conduct inventory audits ranging from monthly to annually to ensure accurate inventory records and detect any discrepancies or potential issues.
Inventory audit risk refers to the likelihood of errors, discrepancies, or fraud related to inventory records and processes. It includes risks such as inaccurate inventory valuation, misclassification of inventory, theft or shrinkage, and inadequate internal controls. Proper inventory audit procedures can help mitigate inventory audit risks and ensure the accuracy and reliability of inventory records.
A slow-moving inventory audit involves reviewing and analyzing items that are not selling as quickly as expected or have been in the inventory for an extended period. This type of audit aims to identify reasons for slow-moving inventory, such as obsolete items, overstocking, pricing issues, or changes in market demand. It helps organizations optimize inventory management practices, reduce holding costs, and improve inventory turnover rates.
Recommended Articles
This article has been a guide to what is an Inventory Audit. Here we explain the procedures, checklist, examples, risks, and objectives associated with the process. You can learn more about excel modeling from the following articles –