Table Of Contents
What Is Plantwide Overhead Rate?
The Plantwide overhead rate is the overhead rate that companies use to allocate their entire manufacturing overhead costs to their line of products and other cost objects. This overhead allocation method finds its place in very small entities with a minimized or simple cost structure.
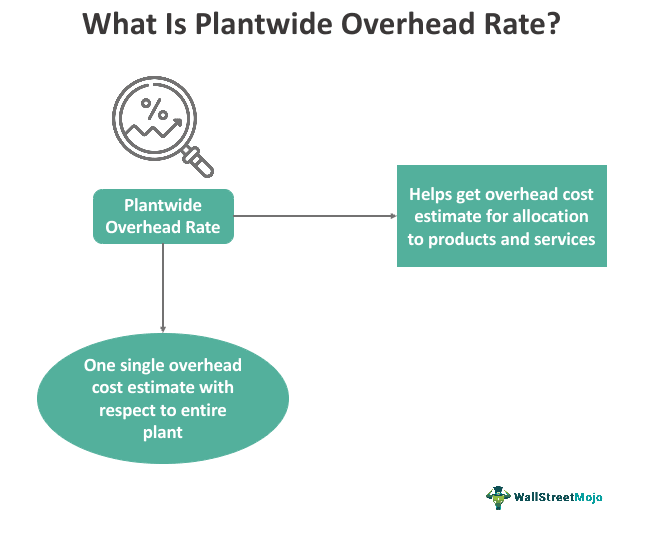
As the name implies, these overhead rates take into account the entire plant and not a particular segment or department. It is one of the simplest forms of resource or cost allocation. The plantwide overhead rate might not help obtain exact figures, but the estimates are efficient enough for better planning.
Plantwide Overhead Rate Explained
Plantwide overhead rate is a method of allocating manufacturing overhead costs to the products and cost objects associated with the business. It is generally suited for small firms and has a simple cost structure. However, there are a few scenarios where its usage is suitable:
- The total sum of the overhead cost to be allocated is not worldly enough. Using multiple allocation rates to drive a higher level of allocation is not needed.
- The various departments present in the company are providing a similar type of service.
- The management accepts using a single allocation base to allocate the entire overhead cost.
On the contrary, a single plantwide overhead rate is not suited for firms where the overhead to be allocated is a mammoth sum, various departments associated with the company are providing different levels and types of services, and lastly, when it is evident that the company must use different types of the allocation base. Therefore, in practical scenarios, it is generally seen companies will avoid its use and instead use a small number of cost pools, which are again separately allocated with different overhead rates. Although it is a time-consuming process, it increases the accuracy of the overall overhead allocation process. Thus, a trade-off between time and accuracy comes in the way of using a single plantwide overhead rate or usage of cost pools.
Formula
The formula that helps us calculate plantwide overhead rate is given below:
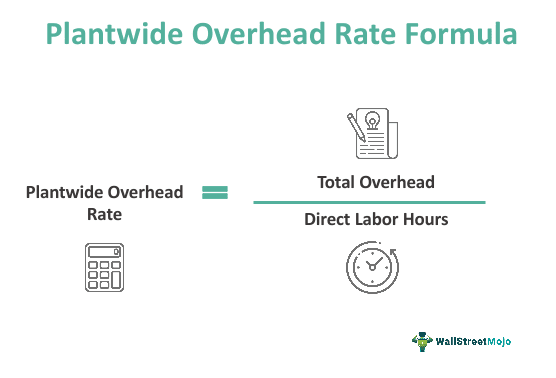
Plantwide Overhead Rate = Total Overhead / Direct Labor Hours
It means the total number of direct labor hours is taken as the denominator, which is divided by the numerator as the total overhead cost of the company.
How to Calculate?
The calculation of the plantwide overhead rate first requires gathering the following information.
- The first and foremost information is required in the total operational cost apart from the direct cost of production. Usually, direct costs are raw materials and direct labor hours. The indirect cost is what we call the overheads.
- We will also require the total number of direct labor hours to produce each product in the company. The per-unit labor cost is calculated by taking the total labor hours and dividing the sum by the number of units manufactured by the company.
- Now coming to the final step of calculation for arriving at our calculation, we need to first divide the business's total overhead by the sum of the additive labor hours put in, which have been consumed to estimate the overhead consumed per hour of labor. After this, the resultant is multiplied by the total labor hours consumed to manufacture per output. Thus, this way, we can arrive at the plantwide overhead rate.
One more approach is to calculate the plantwide overhead rate using an alternative approach or direct cost method. Instead of direct labor hours, we use the direct cost for our calculation. To calculate this, we first need to identify the total direct cost of production and the total overhead cost for the specific period. Thus, this total overhead is divided by the total direct cost to ascertain the single plantwide overhead rate.
Example
Let us consider the following example to understand the concept better:
A company's total overhead cost for a specific month is $100,000. The manufacturing plant requires 1000 labor hours to manufacture 500 units of a specific product, which we assume as product X. The same manufacturing plant also produces 1000 units of another product, which we call product Y, using 500 labor hours. So, the total overall labor hours stand at 1500.
To arrive at the calculation, we need to divide the total overhead of $100,000 by the total labor hours, which is 1500. We find the resultant number as 100,000/1500 = $67 as overhead per labor hour. Therefore, product A will need 1000/500 or 2 hours per production unit. Therefore, the overhead rate for product A is $67*2 = $134/unit. Similarly, product B needs 500/1000 or 0.5 hours per production unit. Therefore, the overhead rate for product B is $67*0.5 = $33.5/unit.
Importance
When plantwide overhead rate is calculated and is known to the entities, they can can plan and allocate overhead costs per the estimates. There are many other aspects that make these rates important for business firms:
- It is best for firms that are small in size and have a uniform cost structure.
- It is easier for firms with a single product offering or for firms where all departments produce similar products or have uniform cost objects.
- It makes the calculation easy as only one rate gets allocated to the product or cost objects.
- It produces more accurate results for firms producing single products than the cost pool method, making the calculation more complicated.
- It is a time-saving process compared to the multiple allocation process or multiple overhead rates.
- Plantwide overhead rate simplifies overhead allocation as only a single overhead rate is used for calculation.
Plantwide Overhead Rate vs Departmental Rate
Both plantwide rate and departmental rate are means of estimating the overhead cost allocation to products and services. However, there are a few points of differences that make each preferable by firms as per their requirements and suitability.
Let us have a quick look at the following differences between these two overhead rates:
- As the names imply, the plantwide overhead rate is an estimate obtained on plant-wise basis, while the departmental overhead cost estimate suggests the allocation of costs based on particular departments.
- In plantwide means, a single overhead cost estimate is obtained. On the contrary, departmental overhead costs provides cost allocation estimates, which is different for different departments.
- Plantwide overhead rate works well for firms with few products and not-very-widely spread businesses. The departmental overhead costs are recommended for firms with multiple products and widely spread reach.
Recommended Articles
This has been a guide to what is Plantwide Overhead Rate. Here, we explain its formula, see how to calculate it along with an example, vs departmental rate. You can learn more about it from the following articles –