Table Of Contents
What Is Total Manufacturing Cost (TMC)?
Total Manufacturing Cost (TMC) refers to the overall money spent on the production activities for processing the raw material into finished goods in a given period (quarter or year). It involves three significant expenses, i.e., direct material cost, direct labor cost, and factory or manufacturing overheads.
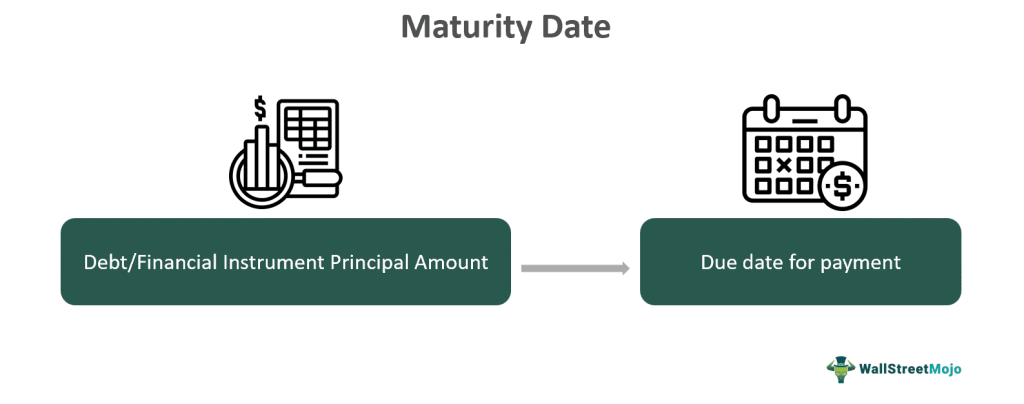
Business entities often review such overheads to determine their profitability and financial health by tracking their factory-level costs. Moreover, such an expense is a crucial factor in determining the sales price of goods. Therefore, it is critical for cost management in manufacturing companies where minimizing the factory overheads results in higher profits, ensuring overall operational efficiency.
Table of contents
- The Total Manufacturing Cost (TMC) is the gross amount a business entity spends on producing certain goods during a given period.
- It comprises the three fundamental cost components, i.e., direct material, direct labor, and manufacturing overheads. Thus, it is computed as the sum of all these three different expenses.
- Its evaluation serves as a critical parameter for managerial decision-making and facilitates the long-term financial planning of the company’s operations while ensuring production efficiency.
- The total manufacturing cost variance is the shortfall or surplus of the actual TMC when compared to the standard TMC.
Total Manufacturing Cost Explained
Total Manufacturing Cost (TMC) is the aggregate of all the factory-level expenses incurred by a company in producing a particular product. It is the foremost consideration for establishing a production unit to determine whether such operations are feasible and would generate profits in the long run. However, it doesn’t account for the administrative and selling expenses.
The TMC involves both direct and indirect manufacturing overheads. It has the following three major cost elements or components:
- Direct Material Cost: Such expenses include purchasing direct raw material consumed for producing the finished item.
- Direct Labor Cost: The labor overheads include the direct compensation, wages, salaries, insurance, etc., paid to the workers engaged in the production and assembly line staff.
- Manufacturing Overheads: These are the indirect expenses incurred at the factory premises that facilitate the manufacturing process, such as energy costs, factory rent, machinery repairs and maintenance, depreciation, insurance and taxes, and other utility expenses. It also comprises indirect material overheads, such as the items required for preserving the raw material from damage. The other factory employees included under this head are warehouse workers, quality assurance staff, etc.
There can be various ways through which a company can manage and control its total manufacturing cost. The foremost consideration is reducing the cost of raw materials through bargaining with suppliers, availing material from new suppliers at a lower cost, and limiting the wastage of these items in the production process. Another measure is curtailing human resource expenses while ensuring higher productivity at the same compensation by reducing idle time or unproductive sessions. Simultaneously, the managers can reduce the indirect manufacturing overheads by saving on utilities.
Formula
Given below is the total manufacturing cost equation commonly used by factory managers to determine the overall money put into the production of goods during a particular period:
Total Manufacturing Cost = Direct Material + Direct Labor + Factory Overheads
Here,
Direct Material = Beginning Inventory + Purchases - Ending Inventory
Direct Labor = Direct Labor Hourly Rate * Direct Labor Hours, and
Overheads = Indirect Material + Indirect Labor + Insurance + Depreciation + Utilities + Taxes
Examples
Let us now have a look at specific examples for understanding the concept of TMC in manufacturing companies:
Example #1
Imagine that a production manager, John, in a furniture manufacturing company analyzes the TMC every quarter to determine the total manufacturing cost variance from the standard or estimated figures. For this purpose, she determines the total manufacturing cost per unit and finds out that the cost of manufacturing a chair has gone up by 10% due to the rise in labor and material costs. This surge in expenses has brought down the overall profit by 8%. Hence, he suggests that top-level management increase the sales price of chairs.
Example #2
Suppose given below is the various cost-related information of a bag manufacturing company:
- Beginning Inventory - $10000
- Purchases - $13000
- Closing Inventory - $8000
- Direct Labor Hourly Rate - $5
- Direct Labor Hours - 1000
- Indirect Material - $2500
- Indirect Labor - $4500
- Rent - $3000
- Electricity Bill - $350
- Labeling Cost - $100
- Depreciation - $200
If the company produces 5000 bags quarterly, determine the total manufacturing cost per unit.
Solution:
For Calculating Total Manufacturing Cost:
TMC = Direct Material + Direct Labor + Factory Overheads
Direct material = Beginning Inventory + Purchases - Ending Inventory
= $10000 + $13000 - $8000 = $15000
Direct Labor = Direct Labor Hourly Rate * Direct Labor Hours
= $5 * 1000 = $5000
Overheads = Indirect Material + Indirect Labor + Electricity Bill + Depreciation + Labeling Cost + Rent
Overhead = $2500 + $4500 + $350 + $200 + $100 + $3000 = $10650
TMC = $15000 + $5000 + $10650 = $30650
On applying the Total Manufacturing Cost Per Unit formula:
TMC Per Unit = $30650 / 5000 = $6.13
Hence, the TMC incurred by the company in a quarter is $ 30,650, while the TMC per unit is $6.13.
Total Manufacturing Cost vs Cost Of Goods Manufactured
The main differences between TMC and cost of goods manufactured (COGM) two are:
Basis | Total Manufacturing Cost (TMC) | Cost Of Goods Manufactured (COGM) |
---|---|---|
Definition | It is the aggregate of all those expenses incurred in the process of making or assembling a particular product in the given period. | It is the expense incurred on completing the production of a particular product in a specific accounting period. |
Scope | Includes all direct and indirect expenses incurred at factory level, I.e., direct material cost, direct labor expenses, and manufacturing overheads | Comprises all direct material costs, direct labor expenses, manufacturing overheads, and changes in inventory |
Calculation | Total Manufacturing Cost = Direct Material + Direct Labor + Factory Overheads | Cost of Goods Manufactured = Direct Materials Cost + Direct Labor Cost + Manufacturing Overhead + Beginning WIP Inventory - Closing WIP Inventory |
Used For | Managerial decision-making and long-term cost planning | Facilitates cost accounting process |
Frequently Asked Questions (FAQs)
It refers to the expenses incurred on manufacturing a single piece of an item. It is computed by dividing the total manufacturing cost in a given period by the total number of units of a particular commodity produced in that period.
The primary aim of evaluating the these costs is to determine the cost of finished goods while analyzing those components that are increasing the production cost. It, thus, helps in cost management and operational efficiency at the factory level.
The total manufacturing cost variance is the negative or positive gap between the actual and the standard manufacturing costs.
The TMC is also called total product cost since it is the aggregate expenses incurred on making or producing a particular item
Recommended Articles
This article has been a guide to what is Total Manufacturing Cost. We explain its formula along with its differences with cost of goods manufactured & examples. You may also find some useful articles here -