Table Of Contents
What Is Production Budget?
Production Budget is financial planning related to the units of product that the management thinks that the business should produce in the upcoming period to match the estimated sales quantity, which is based on the management’s judgment related to the competition in the market, economic conditions, production capacity, consumer prevailing market demands, and past trends.
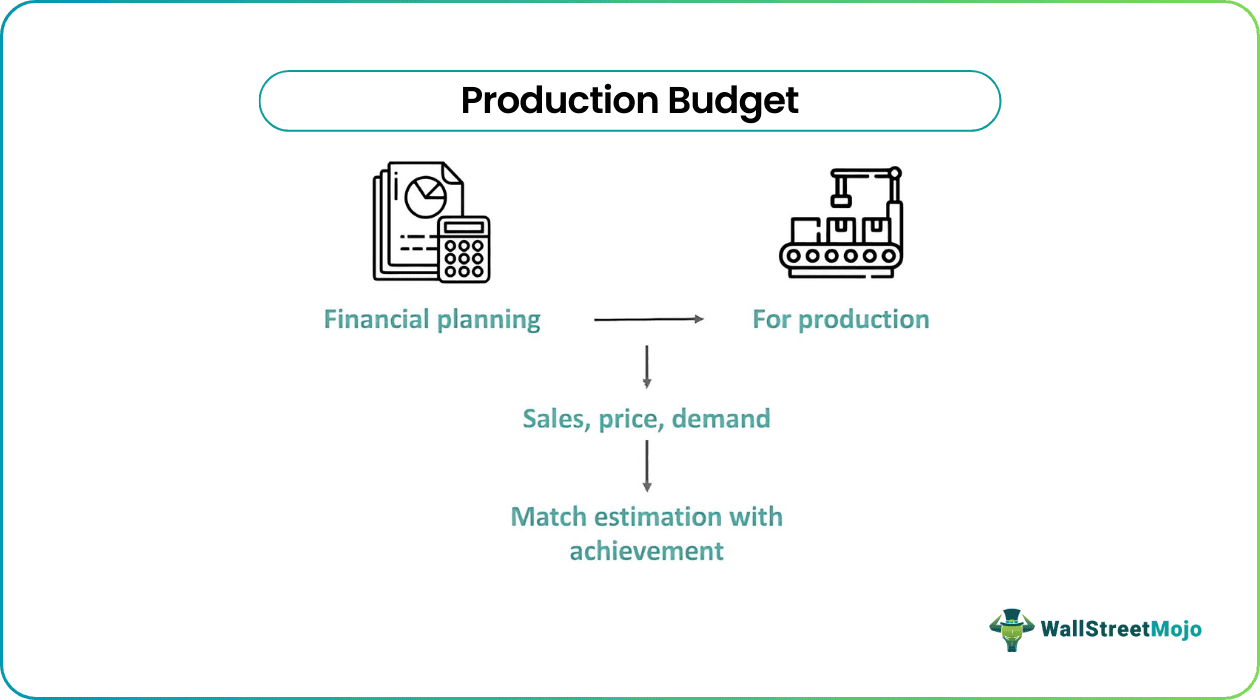
Different organizations in the market adopt different types of strategies and policies. The production budget forecasts the production of the business and gives the targets to employees of the company for achieving the desired output efficiently and incurring minimum expenses. Also, the preparation of this budget is more cumbersome and problematic for the small organization due to the presence of fewer resources, and they can experience more levels of market fluctuations when compared with the large businesses.
Table of contents
Production Budget Explained
The term production budget refers to allocation of funds for the production or manufacturing of goods and services within an organization based on certain plans and strategies adopted by the management. These plans are in turn based on sales target, the revenue and profit target, investment plans, market demand and supply, the economic and political conditions of the country, etc.
It is an important component of every business process and the budget takes into consideration the costs related to raw materials, labor, utility related costs, supply chain management cost, transportation, and so on. The production budget sample is planned in such a way so that there is enough funds to meet the expenses and keep the business running in such a way that the revenue and profit targets are met consistently.
The different important points to the budget are as follows:
- There are mainly three types of components of the production budget, which include the Direct Material budget, the Direct Labor budget, and the overhead cost budget.
- For a company that started working recently and does not have past data and experience, it becomes very difficult to estimate the figures for the production budget sample compared with a business that has existed for a long time because of the availability of the past trends for them.
A comprehensive budget related to production requires a lot of estimation and complex evaluation based on past data. An effective allocation will ensure proper cost management, good understanding and interpretation along with forcasting using tested financial models in order to effectively allocate funds in order to calculate production budget.
Components
Mainly there are three components in the production budget sheet, and they are as follows:
#1 - Direct Material Budget
The Direct Material budget includes the opening inventory of raw materials, purchase cost of raw material, material that goes into production, and closing inventory of raw material that will be incurred to produce the units of product that the organization estimates to produce in the coming period.
#2 - Direct Labor Budget
Direct labor budget includes the cost of labor employed in a production like wages, bonuses, commission, etc., that are expected to be payable to the workers of the business organizations.
#3 - Overhead Cost Budget
All the other costs that don't constitute a part of the material and direct labor budgets are shown in the overhead budget cost. This budget consist of both variable cost as well as a fixed cost.
How To Calculate?
Here we analyse the steps involved in order to calculate production budget.
- Decide the time frame- It is important to understand for what time span the budget is to be designed. This will be decided based on the kind of goods and services, the sales target, how much time it takes for the company to produce a single unit of the product, the market demand, etc.
- Estimation of inventory – The inventory estimation is very crucial because it this is not correct then the production process and profitability can be hampered. Over accumulation of inventory may lead to blocking of funds, wastage and high overhead cost. Less stock will prevent the production process to run smoothly. Therefore, inventory estimation should be done carefully while planning the budget.
- Forecasting sales – The sales figures are estimated in the process, which is required to understand how much or what level of production is to be planned fro a given period so that the sales target is achieved and there is no excess accumulation of finished goods, which increase cost. This will also lead to evaluaton and forcasting or profitability which the organization can aim for.
- Plan production level – The ultimate step is to forecast and evaluate the production level which will help in utilizing the resources in an optimum manner, reduce cost and increase revenue. This production level has to be communicated to different departments of the organization who will plan the necessary action to initiate the process.
It is to be noted that the above steps in the production budget sheet require a lot of calculation and assumptions along with careful analysis of past data and current situation, which act as guidelines for designing the budget effectively.
Example
Let us understand the concept with the help of a suitable example.
XYZ ltd manufactures the bottle and makes the forecast for the upcoming year, which ends in December 2020. It forecasted that the sales in the next year would be $ 8,000 in quarter 1, $ 9,000 in quarter 2, $ 10,000 in quarter three and $ 11,000 in quarter 4. The production manager also plans that the ending inventory will be $ 1,000 at the end of each quarter of the company's production. At the beginning of the quarter, one company's inventory was $ 2,500.
Prepare the necessary production budget of the company XYZ ltd for the coming year ending in December 2020.
Solution
Following is the production budget template of XYZ ltd for the year ended on December 31, 2020.
Production Budget of XYZ ltd for the Year Ended December 31, 2020
Sr. No | Particulars | Quarter 1 | Quarter 2 | Quarter 3 | Quarter 4 |
---|---|---|---|---|---|
A | Sales Unit Forecasted | $8,000 | $9,000 | $10,000 | $11,000 |
B | Planned Ending Units of Inventory | $1,000 | $1,000 | $1,000 | $1,000 |
C | Total Production Required (A+B) | $9,000 | $10,000 | $11,000 | $12,000 |
D | Beginning Inventory of Finished Goods | $2,500 | $1,000 | $1,000 | $1,000 |
E | Units to be Produced (C-D) | $6,500 | $9,000 | $10,000 | $11,000 |
Thus in the above example, the budget prepared shows the calculation regarding the number of units to be produced.
Also, as planned, the production manager's ending inventory units are decreased from $ 2,500 to $ 1,000 even though the company's production is expected to increase every quarter. So it is a risky forecast because a company's safety stock level is cut.
Advantages
- It helps maintain an optimum balance between the sales, inventory position, and production of the company and contributes to the coordination of policies and plans related to them.
- It provides guidance or plan to the organization as it gives the production target that the management of the company expects to be achieved in the upcoming period.
- With the target being set using the production budget, it motivates the company employees to work hard to achieve the goals in time and more efficiently.
- With the help of this budget, the plant and machinery, as well as its labor, can be utilized to the maximum possible extent by the company.
Disadvantages
- Preparing the company's cost of production budget is a time-consuming process as it requires lots of time and effort to manage the company.
- It is based on the judgment and the estimates of the management, so achieving an adequate and accurate level of a forecast of the company's production is not generally possible in the present competitive, unpredictable market.
- Everyone in the organization has different mindsets and ways of thinking, so the different persons in the company may have different opinions about the production budget. In that case, employees of the organization might not be willing to accept this budget, which is prepared by the company's top-level management.
- For a company that started working recently and does not have past data and experience, it becomes very difficult to estimate the figures for the production budget.
Production Budget Vs Material Budget
Both the above concepts are related to the production process but deal with different aspects. Let is study the differences as given below.
- The cost of production budget deals with the number of units of goods that the company should plan to produce to meet the sales target, but the latter deals with raw material procurement cost that is required in the manufacturing process.
- The purpose of the former is to meet he sales and demand are maintaining the correct inventory levels in the organization, but the purpose of the latter is estimation of cost or the raw materials and allocation of fund for the same.
- The components of the former are raw materials, labor, overheads etc, but the components of the latter are only raw materials, that will help in achieving the planned production level.
- The main focus of the former is to plan how much quantity should be produced that will help in achieving the sales target. The focus of the latter is how much quantity of raw material should be procured and should be available in order to support production and help in smooth running of the business.
Thus, the above are some important differences between the two concepts that are widely used in the production process to channelize resources in the right direction.