Table Of Contents
What Is Rough-Cut Capacity Planning (RCCP)?
Rough-cut capacity planning (RCCP) is a strategic method of evaluating whether a company's production capacity aligns with the anticipated demand for a future period. Hence, it helps to identify potential gaps or surpluses in production efficiency to make strategic decisions and adjustments.
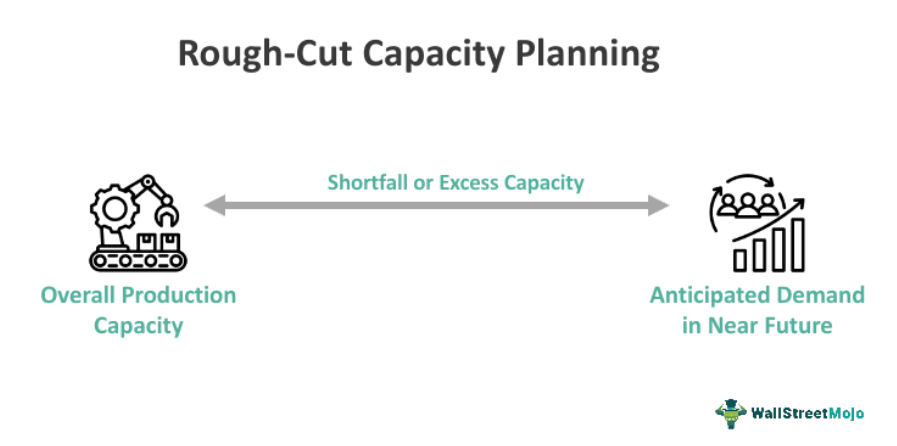
Moreover, such a strategy is often considered a long-term capacity planning technique since it ensures that the company has an optimal stock level, technology, and other resources to fulfill the customer demand in the upcoming period. The process comprises estimating resource needs and availability to validate the master production schedule without going into detailed scheduling.
Table of contents
- Rough-cut capacity planning is a strategic approach for determining the difference between a company's production capacity and the planned production for a specific period, generally weeks or months.
- It enables the feasibility of a master production schedule, facilitates quick assessment, and encourages high-level resource optimization but lacks precision and adaptability in complex or rapidly changing scenarios.
- It differs from the Master Production Schedule (MPS), which outlines a detailed schedule of a specific product while aligning its production with demand and capacity constraints in the short term.
Rough-Cut Capacity Planning Explained
Rough-cut capacity planning is a crucial technique companies employ after the demand planning process and the creation of the master production schedule to ensure that the business is equipped with sufficient resources to fulfill the anticipated demand. The project managers often employ rough-cut capacity planning software and tools to streamline calculations and analysis, aiding in efficient data management and production optimization.
Given below are some basic steps for the RCCP implementation:
- The process begins with analyzing historical data and forecasts to grasp the anticipated product or service demand.
- Next is the assessment of the resource capacity, extending to equipment, labor, and facilities.
- Now comes the identification of differences in current and potential resource utilization to find the gap or excess capacity.
- Then, the manager must break down the expected demand into specific workloads for each resource, estimating production hours, machine time, or other relevant units.
- Gauging the potential challenges that could impact capacity, such as machine downtime, maintenance, or employee availability, is equally important.
- The managers then make variations in demand and resource availability to adjust stock levels to attain a balance between demand and production.
- Capacity planning is an ongoing process and requires regular reviews and updates based on actual performance and changes in demand.
Three primary rough-cut capacity planning strategies include Capacity Planning Using Overall Factors (CPOF), Capacity Bills (BOLA), and the Resource Profile Approach. The CPOF utilizes historical data to estimate workstation capacity based on the Master Production Schedule (MPS). However, capacity bills establish a direct link between workstation hours and MPS quantities, which is especially beneficial for multi-product companies.
On the contrary, the resource profile approach considers activity completion times and lead times, providing a more precise capacity assessment by extending beyond workstation hours.
Examples
While various capacity planning techniques are available, RCCP is considered a sound approach for determining the bottleneck or excess capacity at the initial stage after demand planning. Let us now understand its implication in the real world:
Example #1
Suppose ABC Innovations is gearing up for a software development project next month. Employing rough-cut capacity planning, they analyze initial data to estimate production requirements, revealing potential hurdles like a shortage of engineers and restricted tool accessibility.
In response, ABC Innovations strategically addresses these challenges by hiring new talent, investing in training programs, and contemplating tool subscription upgrades to align with the anticipated demand. The application of rough-cut capacity planning proves instrumental in early bottleneck identification during the planning phase, enabling proactive measures for optimizing production efficiency.
Example #2
Suppose in an eyewear manufacturing company, the workload according to the planned production for the first quarter of 2024 is as follows:
Particulars | January | February | March | Total |
---|---|---|---|---|
Workload from Goggles | 2000 | 2000 | 2000 | 6000 |
Workload from Glasses | 5000 | 5000 | 5000 | 15000 |
Total Workload | 7000 | 7000 | 7000 | 21000 |
Available Capacity | 6400 | 7200 | 6900 | 20500 |
Delta or Difference | -600 | 200 | -100 | -500 |
For January 2024, if we determine the weekly capacity, it will be
Production line required capacity (weekly) = 7000/4 = 1750
Production line available capacity (weekly) = 6400/4 = 1600
And, production line capacity load ratio (weekly) = Production line required capacity (weekly) / Production line available capacity (weekly)
= 1750/1600 = 1.09
The load ratio greater than 1 (1.09) indicates that the production line operates slightly beyond its available capacity. In this context, a load ratio exceeding 1 suggests a production gap, and the company needs to boost its production capacity to fill this gap and meet the demand more effectively.
Pros And Cons
Rough-cut capacity planning is often considered suitable for making the necessary changes to the master production schedule to determine the optimal resource requirement. While it has multiple advantages, certain drawbacks cannot be overlooked. Let us discuss all of these below:
Pros
- Comprehensive Overview: RCCP provides a broad understanding of resource availability and potential constraints at a macro level.
- Early Identification of Potential Issues: Since it is performed at the early stage of production, it facilitates spotting the potential capacity issues before it's too late, thus allowing for a proactive problem-solving approach.
- Sensible Decision Making: As RCCP allows a proper assessment of resource requirements and capacity constraints, the companies can make better decisions pertaining to employees' training, working hours, budget, technology required, and inventory.
- Resource Optimization: RCCP enables better utilization of resources by aligning them with demand forecasts, thus ensuring the availability of sufficient raw material, labor, and capacity to attain maximum production efficiency.
- Cost Reduction: Optimizing resource allocation and minimizing idle time contributes to cost curtailment and higher profitability.
Cons
- Data Quality: Since RCCP significantly relies upon the production schedules planned by the project managers and other manual data collection and reconciliation, any discrepancies in such inputs can result in inaccurate outcomes.
- Dependency on Estimates: It depends heavily on estimates and assumptions, which can be inaccurate and may lead to deviations from actual capacity needs.
- Inability to Handle Dynamic Changes: As a long-term production planning technique, it is unsuitable for responding to sudden shifts in demand or resource availability, making it less effective in dynamic environments.
- Calculation Errors: The RCCP technique involves a lot of calculation, which is a task for a mathematically-learned individual.
- Time-Consuming: If the organization operates on a large scale, implementing RCCP requires ample time and effort. However, the emergence of various planning tools and software has overcome this limitation.
- Communication Barriers: While this approach requires data collection from different departments or units at different geographical locations, miscommunication and disruptions can occur.
Rough-Cut Capacity Planning vs Master Production Schedule
Rough cut capacity planning (RCCP) and master production schedule (MPS) serve varying roles in production planning; let us see how:
Basis | Rough-Cut Capacity Planning | Master Production Schedule |
---|---|---|
Definition | RCCP is a long-term capacity planning technique that assesses overall resource requirements for fulfilling the potential future demand. | MPS is a systematic approach to identifying whether the existing production capacity is adequate to satisfy the demand for a specific product in the short term. |
Focus | Considers high-level resources such as labor, machinery, and facilities | Concentrates on specific products and timeframes, detailing what, when, and in what quantities to produce |
Objective | Offers a broad view of capacity requirements for anticipated production levels | Specifies the quantity and timing of production to meet the demand outlined in the sales and operations plan |
Flexibility | Allows flexibility in adjusting the production plan to accommodate capacity constraints | Offers a more rigid schedule focused on meeting precise production requirements. |
Timeframe | Covers a more extended time horizon, often spanning weeks or months | MPS generally covers shorter spans, often weekly or daily |
Level of Details | Provides a high-level overview of capacity needs without detailed product-specific information | Provides specific details for individual products, including production quantities and timing |
Integration | RCCP validates MPS | MPS closely links with customer demand, inventory levels, and overall production capacity. |
Frequently Asked Questions (FAQs)
Rough-cut capacity planning is crucial for businesses as it provides a preliminary assessment of production capacity against anticipated demand. Offering a high-level overview enables early identification of potential constraints, facilitating proactive decision-making. This strategic approach ensures optimal resource allocation, minimizes inefficiencies, and aligns production capabilities with market demands, enhancing operational efficiency and customer satisfaction.
Capacity requirements planning (CRP) gauges the feasibility of the production capabilities pertaining to labor and machines when compared with the potential demand for products or services. In contrast, rough-cut capacity planning provides an initial, high-level overview of capacity at an aggregate level, aiding in the identification of potential constraints and imbalances in overall capacity.
The RCCP technique is widely used in manufacturing and production units to balance production capacity and market demand for products or services while ensuring no inefficacies or excess resources.
Recommended Articles
This article has been a guide to what is Rough-Cut Capacity Planning. Here, we explain its examples, comparison with master production schedule, & pros and cons. You may also find some useful articles here -