Table Of Contents
What Is Carrying Cost Of Inventory?
Carrying Cost of Inventory refers to the expenditure businesses make to hold inventory in their warehouse during a given accounting period. The purpose of computing this amount is to find the total cost a company is required to bear till it can sell off this inventory and convert the investment into sales proceeds.
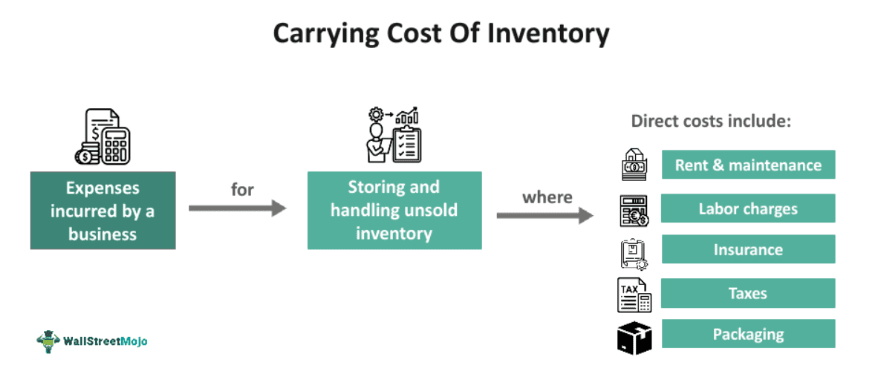
Direct expenses include storage costs, depreciation, insurance, spoilage, taxes, and handling costs. Indirect costs are shrinkage, pilferage, theft, etc. When inventory remains unsold, it blocks a company’s capital. It also indicates that there might be a mismatch between production and demand. Due to this, the chances of making money and posting profits within a given accounting period typically decline.
Table of contents
- Carrying Cost of Inventory is the money companies spend to store and maintain inventory/stock in warehouses. It is also called holding cost.
- This cost is shown as a percentage, and it is obtained by dividing the total inventory holding cost by the total inventory value.
- The average inventory holding cost ranges between 15% and 30%. However, it can differ across industries.
- The various components that make up inventory holding costs are capital, insurance, handling, labor charges, etc. If inventory planning & control is ineffective, all associated expenses increase.
Carrying Cost Of Inventory Explained
The carrying cost of inventory is a vital aspect of efficient inventory management. Since it is a significant expenditure, these costs can become a financial burden on a company holding inventory in its warehouse. It is usually expressed as a percentage of the total inventory value. If a business incurs high inventory carrying costs, it shows inventory is steadily piling up in the warehouse. Such inventory takes up storage space and negatively impacts sales.
The following are some reasons why inventory may have to be stored in warehouses:
- Seasonal demand: If a company produces goods that customers demand only in specific seasons, such stock needs storage.
- Ineffective demand forecasting: If production is based on incorrect estimates, the inventory holding period inevitably increases.
- Inefficient procurement: If procurement and replenishment strategies are faulty, storing raw materials and finished goods (as a consequence) becomes unavoidable.
- Additional stock: Some companies store finished goods to avoid stockouts.
- Defective or expired products: If products have expired or are defective, they need to be dealt with immediately to prevent hikes in carrying costs.
- Other reasons: Inventory holding costs go up due to multiple other factors like long supply chains, return & refund processing, inaccurate sales estimates, etc.
The average carrying cost of inventory is around 15% to 30%. However, it can differ across companies and industries. If the inventory carrying cost is high, it means that firms anticipate more demand, and hence, they keep more inventory in their warehouses. As a result, the associated storage costs also increase. Low carrying costs generally depict stability where a company holds adequate inventory. In short, the more time the inventory stays on the shelf, the more the cost increases. Achieving optimal inventory is every company’s goal.
Another important aspect that requires our attention is compliance—statutory and internal. Unless a company manages its inventory well, including keeping the carrying costs under control, it might unintentionally violate the compliance requirements related to accounting, financial reporting, and taxation. Also, complying with internal inventory management processes and industry best practices is tough without effective carrying costs control. It can have a ripple effect on various aspects of the business, such as sales, production, procurement, logistics, warehousing, etc.
Components
Several elements make up the carrying cost of inventory. Let us study them in this section.
- Capital cost: This refers to the funds used to store, maintain, and move the inventory. It is a major chunk of the total carrying costs. It also represents the opportunities a company loses by not investing the money tied up in inventory for other growth endeavors.
- Insurance and depreciation: Insurance is a significant expenditure companies are required to incur to protect their inventory from various disasters and calamities as specified in the policy they buy. The higher the inventory holding period, the higher the insurance expense. Depreciation refers to the declining value of the stored inventory. The longer it takes to sell such inventory, the higher these costs go.
- Storage cost: Storing inventory requires a considerable investment. A proper facility, rented or owned, requires companies to bear storage costs. Depending on the goods being stored, these costs typically differ. For instance, items that need a cold storage facility may become quite expensive to handle if they are not sold off within a specified period.
- Handling cost: Handling refers to moving and managing items in inventory in a warehouse. Handling costs usually include labor charges, maintenance equipment costs, etc. Other costs related to maintaining goods in a warehouse include payments to supervisors and security staff.
- Shrinkage cost: This refers to situations where damage, theft, or fraud impacts the inventory volume and its resultant value. Such losses mean that the products or goods will not reach customers. This is a direct loss of sales proceeds.
- Physical inventory counting and audits: A company’s inventory tracking mechanism involves audits at regular intervals. Excessive inventory increases the costs associated with these activities.
- Taxes: Firms are required to pay taxes in line with the regulations of the region in which they operate. Excess inventory attracts high expenditure in the form of taxes at the various stages of stock processing.
Companies may be required to include other costs based on their business activities and operating models.
How To Calculate?
In this section, let us discuss the carrying cost of inventory formula.
Carrying cost of inventory = (Total inventory holding costs/Total inventory value) X 100
The total inventory holding costs comprise all the expenses pertaining to storing, maintaining, and moving the inventory in a given accounting period. Some common expenses include employee salaries, storage costs, service charges (utilities, rent, security, etc.), and depreciation costs. Inventory value is the monetary value of the total stock held in a warehouse. The carrying cost of inventory is a percentage of the total inventory value in a given accounting period.
The first step involves calculating the total inventory holding costs and the total inventory value for a given period. The total inventory holding cost figure is then divided by the total inventory value. This number is multiplied by 100 to obtain the result in the percentage form.
Examples
Let us study a few examples in this section.
Example #1
Suppose Anne is employed as a supervisor at Paper Plants Ltd. Over the years, various suppliers in the market have purchased this company’s products. However, the company saw a drop in sales in the last quarter of 2023. As part of her responsibilities, Anne calculated the inventory holding costs. She considered the following items for this calculation.
- Storage costs = $15000
- Wages = $7000
- Insurance = $30,000
- Handling cost = $2000
- Annual inventory value = $100,000
Carrying cost of inventory = (Storage costs + Wages + Insurance + Handling cost) / Annual inventory value * 100
= ($15000 + $7000 + $30000 + $2000) / $100,000 * 100
= $54,000/ $100,000 * 100
= 54%
The average carrying cost of inventory was 54%, which was above the standard range of 15-30%. It indicated that the business could not convert its inventory into sales efficiently.
Example #2
A December 2023 report talks about how water shortages in the Panama Canal have affected shipping operations in the region. The low water level triggered the need to contain logistics, and shipping operations were reduced by 33%.
The administrator of the Panama Canal Authority, Dr. Ricaurte Vásquez Morales, highlighted the various factors impacting international trade apart from natural causes like water shortage. He expressed apprehension about the rising interest rates causing inventory carrying costs to increase worldwide.
He also indicated that innovative measures would have to be adopted to ensure inventory storage costs stay under control. He also emphasized that it is imperative that goods reach their destination on time if companies wish to avoid high inventory-related expenses, including the carrying cost of inventory.
Frequently Asked Questions (FAQs)
The following are some reasons to calculate inventory carrying costs regularly:
- It allows companies to make the right inventory management decisions, plan production activities, prevent stockouts, and increase sales.
- It facilitates proper inventory accounting and ensures compliance.
- It helps companies estimate their profits and profitability in a given accounting period.
Companies can reduce their inventory costs and improve results by following effective inventory management practices, implementing good procurement and logistics processes, developing useful forecasts, predicting demand patterns well, boosting sales efforts, and conducting regular audits, among other things.
It is not directly recorded in a company’s financial statements. However, it appears on the income statement as part of the Cost of Goods Sold (COGS). Though it is not recorded as an independent item, there are several metrics that tell management how successful their company has been in handling inventory.
Recommended Articles
This article has been a guide to what is Carrying Cost Of Inventory. Here, we explain the concept along with how to calculate it, its examples, and components. You may also find some useful articles here -